نقش شرایط زمین شناختی در طراحی تونل:
1- چین خوردگی: وجود چین خوردگی در سنگ سبب کاهش مقاومت آن می شود و در اثر احداث تونل ممکن است درز و شکافهای بیشتری را در سنگ سبب شود.
2- گسل: وجود گسل سبب ایجاد صفحات شکستگی در سنگ می شود که پس از حفر تونل احتمال لغزش قطعات سنگ را به دنبال دارد.
3- آب زیرزمینی: وجود آب زیرزمینی از جمله مسائلی است که علاوه بر آنکه عملیات تونل سازی را با مشکل مواجه می سازد خطراتی را نیز در پی دارد.
مواردی که در بالا اشاره شد از جمله مهمترین مسائلی بود که در طراحی تونل نقش دارند ولی مواردی مانند زمین های آماس پذیر، درزه ها، گازهای موجود در سنگ ها، دمای سنگها، زمین های رانشی و ... نیز در طراحی تونل ها نقش دارند که از اهمیت کمتری برخوردارند.
صنعت تونل ایران
سالهای طولانی است که متخصصان و کارگران زحمتکش ایران زمین در صنعت تونل آثار ارزشمندی را به تمدن بشری اهدا نمودهاند بطوریکه از چند هزار سال پیش تونلهایی موسوم به قنات حفر میشده است که یکی از ابتکارات شگفتانگیز ایرانیان است. طول بعضی از این سازه های زیرزمینی به 70 کیلومتر می رسد. تعداد قناتهای ایران بالغ بر 5000 رشته بر آورد شده و جالب توجه آن است که این قناتهای متعدد، طویل و حساس از لحاظ جهت و شیب با وسایل بسیار ابتدایی حفر شدهاند. قدیمیترین آثار و قنات که در دنیا کشف شده و باستانشناسان ردیابی و کاوش کردهاند، ناحیهای در شمال ایران است که قدمت آن به حدود سه هزار سال قبل یعنی دوره ورود آریاییها میرسد. در دوره معاصر و ابتدای قرن سیزدهم هجری احداث اولین تونلهای راه وراهآهن در دستور کار دولت ایران قرار گرفت.بر اساس برنامههای پنج ساله و بالاخص چشم انداز بیست ساله برنامههای توسعه کشور، نیاز به ساختارهای زیربنایی در کشور بیش از پیش تجلی میکند.
با توجه به شرایط اقلیمی و جغرافیایی کشور و توسعه و گسترش شهرها و مراکزصنعتی ، تونل و فضاهای زیرزمینی برای استفادههای حمل و نقل داخل و خارج از شهر، انتقال آب و فاضلاب ، لوله رانی بدون حفاری سطحی برای انتقال مواد سوختنی و انرژی از قبیل نفت و گاز ، احداث فضاهای زیرزمینی استراتژیکی و دفاعی ، تولید برق ، ایستگاههای مترو و پارکینگ بهطور فزایندهای در حال مطالعه ، ساخت و یا بهرهبرداری هستند. عوامل زمینشناسی و اقتصادی در گذشته از جمله موانع توسعه فضاهای زیرزمینی بوده است. با توجه به توسعه علم و فناوری در مطالعات زمینشناسی و مهندسی ژئوتکنیک وآشنایی بهتر و بیشتر با شرایط زمین و ساخت و گسترش تجهیزات ساخت و بهرهبرداری تونلها باعث شده است که رویکرد به این ساختار زیرزمینی بیشتر شود. اغلب شهرهای بزرگ توانایی و گنجایش داشتن حمل ونقل روی سطحی را نداشته و در نتیجه به سیستم های زیر زمینی از قبیل مترو روی آورده و بدون دستخوردگی در سطح زمین ، با احداث خطوط متعدد مترو، شبکه وسیعی از حمل و نقل را در شهرها ایجاد نمودهاند. برای انتقال آب وفاضلاب نیز مشابه حمل و نقل گزینهای به جز استفاده از مجاری زیرزمینی وجود نداشته و شبکههای بزرگ و گسترده تونلهای آب و فاضلاب شهری در حال احداث می باشند. در حال حاضر در کشورهای توسعه یافته در برخی موارد، فضاهای زیرزمینی به عنوان تنها گزینه مناسب برای ایجاد فضاهای تفریحی ، فرهنگی و ورزشی مطرح میباشند. در اغلب موارد فضاهای زیرزمینی در دراز مدت با صرفه تر خواهد بود. از مزایای استفاده از فضاهای زیرزمینی و تونلها ،میتوان به موارد زیر اشاره کرد:
- حفظ محیط زیست
- تأمین ایمنی و امنیت بیشتر
- صرفهجوئی در هزینههای تأمین انرژی
- صرفهجوئی در هزینههای بهرهبرداری و نگهداری
- صرفهجوئی در هزینههای جابجائی تاسیسات شهری و هزینه تملک و خرید زمین
از جمله تونلهای در حال ساخت کشور به موارد زیر می توان اشاره کرد:
الف- تونلهای راه: آزاد راه تهران-شمال(تالون،البرزو...) ، امام زاده هاشم ، تهران-رودهن ، تنگه هیچان-سرخه .
ب- تونلهای راه آهن و مترو: قطعه چهارBیزد-هرمزگان ، متروی شیراز ، متروی تبریز ، خط تهران-کرج(خط پنج) ، خط 3و4 متروی تهران ، متروی اصفهان خطAشمالی وجنوبی ، متروی مشهد .
ج- تونلهای انحراف و انتقال آب: کوهرنگ3 (چارمحال وبختیاری) ، گاوشان(کردستان) ، چشمه لنگان(اصفهان) ، انتقال آب دز به قمرود ، رباط کریم تهران ، خیام و خروجی تهران ، سد کوثر(خوزستان) ، سد کرج به تهران ، نوسود کرمانشاه ، سولکان کرمان ، چشمه روزیه سمنان ، قشلاق سنندج ، سبزکوه(چهارمحال و بختیاری) ، روانسر کرمانشاه ، سد نسای کرمان وآبرسانی بوشهر
د- تونلهای معدنی: ضرورت تأمین مواد معدنی در راستای برنامههای توسعه و سیاست های دولت ، حفر فضاهای گسترده زیر زمینی را ایجاب می نماید که از آن جمله می توان به معدن زیر زمینی زغال سنگ مرکزی طبس اشاره کرد که استخراج آن به صورت مکانیزه طراحی شده و برآورد تولید سالیانه آن 5/1میلیون تن می باشد.
دولت ایران نیز با توجه به کمبودها و نیازبه فضاهای زیرزمینی در رابطه با کاربردهای مختلف آنها ، سرمایهگذاری در بخش تونلسازی را بالاخص در سالهای اخیر مورد توجه قرار داده و از جمله تحولات مهم چند سال گذشته صنعت تونل ایران احداث فضاهای زیرزمینی را با کاربردهای متفاوت در احجام و طولهای بسیار زیاد می باشد. بهطورکلی امروزه دولت در قالب وزارتخانه های نیرو ، راه و ترابری ، صنایع و معادن و کشور(شهرداریها) به طور عمده و وزارتخانههای دفاع ، نفت و جهاد کشاورزی به میزان کمتر به احداث سازههای زیرزمینی میپردازد. به تازگی در تمامی این سازمانها با تصویب قوانین و ایجاد امکان عقد قراردادهایی با ساختارهای متنوع امکان مشارکت شرکت های خارجی وداخلی در سرمایهگذاری و اجرای پروژه فراهم شده است. از دیگر اقدامات جدید انجام شده می توان به حضور موثر و بی سابقه متخصصان داخلی در پروژههای مختلف احداث فضاهای زیرزمینی اشاره داشت و بعضی در زمره بزرگترین سازههای زیرزمینی در دست احداث جهان می باشند که با رعایت استانداردهای جهانی و با طراحی واجرای کارشناسان ایرانی به انجام می رسد.
تونلسازی سیری
در روش تونلسازی سپری متعارف و معمولی قطر تونل از ابتدا تا به انتها ثابت میماند ولی با این حال مواردی است که مانیاز مند افزایش قطر موجود در نواحی خاصی از تونل میباشیم در چنین مواردی قبل از معرفی روش گسترشی ما مجبور به ایجاد مقطع با استفاده از کند و آکند و یا روش ناتم بودیم که البته آن هم باید پس از بهسازی توده سنگ در مقیاس بزرگ انجام میگرفت ...
در ابتدا این روش برای ایجاد و حفر تونل در زمینی نرم و از زیر رودخانه استفاده شد شیوه عملیات مبتنی بود بر فشار و فرو بردن استوانه ای فلزی و انعطاف ناپذیر در داخل خاک و سپس ایجاد ساختار تونل به طورکل عملیات شامل فرو راندن سپر در داخل خاک و ایجاد لاینینگ از پشت سر سپربود به این طریق تونل در آن شرایط و بدون ریزش و تخریب در سطوح بالایی تونل مورد نظر حفر شد که البته رانش سپر در داخل توده خاک توسط جکهایی قابل اجراست . این کار در 1823 در زیر رودخانه thames لندن اجرا شد که سطح مقطع سپر به کار رفته نیز مستطیل شکل بود طراحی مقطع دایروی برای سپرهای مذکور در سال 1869 و از جانب Greathead James Henry مهندس انگلیسی ارائه شد استفاده از سگمنتهای فولادی خاکریزی ونیز تزریق از سوی او در پروه اش به کار برده شد همانگونه که گفته شد سپر جسمیاست فولادی معمولاًبه شکل استوانه که از ریزش مواد به داخل تونل جلوگیری کرده و خود را به جلو و داخل زمین میراند. انواع سپرها عبارتند از :
? سپرهای باز
? سپرهای کور
? سپرهای تعادل فشار خاک
? سپرهای گل آبی
میتوان گفت که کشور ژاپن نقشی عمده در توسعه این روش داشته است در تونلهای احداث شده در شهرهای بزرگ ژاپن به دلیل اینکه اکثرا در زمینهای سست بوده و همچنین به دلیل تراکم رفت و آمد در مناطق پر ترافیک و شلوغ بیشتر به روش سپری حفر شده اند . این کشور همچنین در امر طراحی و ساخت انواع سپرها و ماشین آلات سپری بسیار پیشرفته میباشد.
از روش تونل سازی سپری در اواخر دهه شصت قرن نوزدهم و برای احداث تونلهای زهکشی و فاضلاب استفاده شد و بعد از آن نیز برای ساخت انواع دیگر تونلها نظیر تونلهای کابلهای انتقال برق و همچنین برای احداث تونلهای زیرزمینی و مترو که از آن به عنوان روش ایجاد تونل در مناطق شهری یاد میشود تعمیم یافت.
دلایل استفاده از این روش:
با استفاده از روش تونلسازی گسترشی یا همان روش توسعه ی تونلهای ایجاد شده به روش سپری ما میتوانیم قطر تونل موجود را افزایش دهیم .
در روش تونلسازی سپری متعارف و معمولی قطر تونل از ابتدا تا به انتها ثابت میماند ولی با این حال مواردی است که مانیاز مند افزایش قطر موجود در نواحی خاصی از تونل میباشیم در چنین مواردی قبل از معرفی روش گسترشی ما مجبور به ایجاد مقطع با استفاده از کند و آکند و یا روش ناتم بودیم که البته آن هم باید پس از بهسازی توده سنگ در مقیاس بزرگ انجام میگرفت.
اصول روش ناتم در تونل سازی
روش تونلسازی اتریشی (NATM)، در فاصله سالهای 1957 تا 1965 در اتریش ابداع گردید. نام این روش در سال 1962 در سالزبورگ و جهت تمیز از روش قدیمی تونملسازی اتریشی اعطا گردید. نخستین ارائه دهندگان این روش Ladislaus von Rabcewicz, Leopold Müller و Franz Pacher بودند. ایده نخستین این روش عبارت است از استفاده از فشارهای زمین شناسی در برگیرنده توده سنگ جهت مقاوم سازی ونگهداری تونل.
باید گفت که امروزه مطالعات گسترده ای از سوی متخصصین علم مکانیک سنگ در ارائه طرحی مطمئن برای نگهداری فضاهای زیرزمینی صورت می گیرد که بتواند سیستم نگهداری را به گونه ای طراحی کند که علاوه بر ایمن بودن، از نظر اقتصادی نیز معقول باشد. نتایج این مطالعات بر ضرورت بکارگیری روشهای مشاهده ای همچون NATM در تونلسازی تاکید دارد.
? ویژگی های اساسی ناتم :
ناتم روشی است مبتنی بر تابع نگاری رفتار توده های سنگ تحت بار و مونیتورینگ عملیات ساختمان زیرزمینی سنگ. واقعیت اینست که ناتم به عنوان یک مرحله از حفاری و نیز تکنیک های نگهداری مطرح نیست. ناتم بر هفت ویژگی استوار است:
1- بسیج مقاومت توده سنگ: این متد بر مقاومت ذاتی توده سنگ پیرامون به عنوان یک جز اصلی نگهداری شده در تونل، تکیه می کند. تکیه گاه اولیه طوری هدایت می شود که سنگ را قاد رسازد تا بر خودش تکیه کند.
2- حمایت شاتکریت: سست کردن و نیز تغییر شکل بی اندازه سنگ می بایست به حداقل برسد. این امر با مهیا کردن لایه های نازک شاتکریت بلافاصله پس از پیشروی جبهه کار حاصل می اید.
3- اندازه گیری: هرگونه تغییر شکل ناشی از حفاری باید اندازه گرفته شود. ناتم به نصب تجهیزات اندازه گیری در سطح بالایی نیاز دارد. این در آستر، زمین و گمانه ها جاسازی می شود.
4- تکیه گاه انعطاف پذیر: آسترگیری اولیه نازک است و شرایط لایه بندی اخیر را بازتاب می دهد. این مدل به کارگیری، نسبت به تکیه گاه مجهول سریعتر به کار می اید و موثر می شود. مقاوم سازی با یک آستر بتنی ضخیم به دست نمی اید بلکه با یک ترکیب منعطف از پیچ سنگ، سیم تنیده و شیارهای فولادی حاصل می گردد.
5- بستن وارونگی: بستن سریع وارونگی و ایجاد حلقه حامل بار دارای اهمیت است. این امر در تونلهای حفر شده در زمینهای نرم بسیار وخیم است، جایی که هیچ مقطعی از تونل نباید بطور موقت رها شود.
6- ترتیب قراردادی: دانش ناتم بر اساس اندازه گیری مونیتورینگ پایه ریزی شده است. تغییر در متد تکیه گاه و ساختمان امکان پذیر است. این تنها در شرایطی ممکن است که سیستم قراردادی فادر به تغییرات باشد.
7- اندازه گیری پشتیبانی رده بندی توده سنگ: رده های اصلی سنگ برای تونل و پشتیبانی متناظر آن موجود است. اینها برای هدایت در زمینه تقویت تونل بکار می روند.
اصول کلی ناتم:
تونلزنی به روش جدید اتریشی در خاکهای سست تا سنگ های سخت و مقاوم و در اعماق کم (در جهت به حداقل رساندن نشست سطح) تا اعماق زیاد و بیش از 1000 متر تحت میدانهای تنش ناشی از عملیات معدنکاری انجام گرفته است.
بنابراین اصول زیر به طور کلی قابل اعمال می باشند. این اصول در مقاله آقای دکتر فکر به ترتیب زیر آورده شده است:
? عنصر اصلی باربری یک تونل، توده سنگ پیرامونی آن می باشد.
? بنابراین یکی از اصول عبارت می باشد از: حفظ مقاومت اولیه سنگ تا آنجایی که امکان داشته باشد.
? اتساع یا جابجایی ها باید به حداقل رسانده شود زیرا موجب پایین آوردن مقاومت می گردد.
? وضعیت تنش تک محوری یا دو محوری، شرایط نامناسب برای تونل بوده و باید از آن اجتناب گردد.
? دگرشکلی ها باید به طرزی تحت کنترل دراید که توده سنگ پیرامون تشکیل یک حلقه باربر حول تونل را بدهد. به گونه ای که از
دست رفتن مقاومت به وسیله اتساع در سطحی قابل قبول نگهداشته شود. با اجرای خوب این کنترل، ایمنی واقتصاد افزایش می یابد.
? برای رسیدن به این منظور، تکیه گاه اولیه می باست در زمان درست نصب گردد.
? عامل زمان ویژه سیستم ترگیبی سنگ به اضافه تکیه گاه اولیه، باید به صحت کافی تخمین زده شود.
? تخمین عامل زمان بستگی دارد به :
الف : آزمونهای آزمایشگاهی
ب : آزمونهای برجا
ج : رده بندی توده سنگ
از این سه نرخ دگرشکلی و زمان پابرجایی می تواند استنتاج شده و با رفتار واقعی تونل در حین ساختمان تطبیق و کنترل گردد.
? هرجا که دگرشکلی ها زیاد بود و یا سست شدن توده سنگ انتظار می رود، می بایست از تماس کامل تکیه گاه اولیه با جدار تونل در محل برخورد اطمینان حاصل اید. این امر با بکار گرفتن شاتکریت به بهترین نحو حاصل می گردد.
? تکیه گاه اولیه باید نازک و دارای صلبیت خمشی پایین باشد، از این رو گشتاورهای خمشی پایین آورده و وقوع شکستگی ها در اثر خمش به حداقل می رسد.
? افزایش نگهداری با شبکه توری اضافی، قابهای فولادی، سیمهای فولادی، سیم مهارها یا میل مهارها حاصل می اید نه با آسترگیری ضخیمتری نوع و مقدار تکیه گاه و زمان نصب، از نتایج اندازه گیری دگرشکلی ها تعیین می گردد.
? از نظر استاتیکی تونل را می توان لوله ای ضخیم (یا حلقه ای دوبعدی) که از توده، سنگ و آسترگیری تشکیل یافته در نظر گرفت.
? از آنجا که یک لوله مساعدترین ویژگی پایداری را بدون آنکاه درز داشته باشد داراست، بستن همزمان کف تونل در هنگامیکه سنگ دارای مقاومت کافی نباشد دارای اهمیت است.
? رفتار توده سنگ با بستن به موقع کف تونل تعیین می گردد. پیشروی های زیاد در طاق منجر به دیر بسته شدن کف و آنهم منجر به تشکیل لوله نیمه آسترگیری اولیه گردیده که نتیجه آن بروز گشتاورهای بزرگ خمشی در جهت محور تونل می باشد که منجر به ایجاد تمرکز تنش زیاد در سنگ، در پای دیواره های جانبی می گردد.
? حفاری پیشانی کامل، بهترین روش برای دستیابی یک توزیع یکنواخت تنش است. هر چند که در سنگهای سست، حفاری بخش بخش، برای پایداری در حین ساختمان ممکن است لزوم پیدا کند.
? روند حفاری و نگهداری برای پایداری مهم می باشد. زیرا آنها عامل زمان توده سنگ را تحت تاثیر قرار می دهند.
تغییر در طول دوره حفاری، زمان بستن کف، طول پیشروی طاق، مقاومت و زمان نصب تکیه گاه تماما به طور سیستماتیک برای کنترل فرایند توزیع مجدد تنش و پایدارسازی به کار گرفته میشوند.
? در موارد آستربندی مضاعف، آستربندی نهایی باید همچنان نازک باشد. تنش عمود می باید بر روی تمام سطح تماس بین آستربندی ها منتقل گردیده و تنش برشی در سطح برخورد می باید پایین باشد.
? کل سیستم، توده سنگ به اضافه پوشش می بایست با نگهداری اولیه پایدار گردند.
در صورت خورنده بودن آبهای زیرزمینی آستربندی نهایی می بایست قادر به پایدار سازی توده سنگ به تنهایی باشد. سیم مهارها تنها می توانند به عنوان یک نگهدارنده دائمی تلقی گردند، البته در صورتی که از گزند خورندگی در محیطهای خاص در امان باشند.
? برای کنترل ایمنی سازه تونل، اندازه گیری تنش بتن و تنش برخورد در مرز بین سنگ و آستربندی ضرورت دارد. اندازه گیری دگرشکلی ها همچنان ادامه پیدا می کند.
? فشار ایستایی آب بر روی پوشش و فشار جریان در توده سنگ با زهکشی مناسب پایین آورده می شود.
به طوری که از این اصول دریافت می شود، ناتم روند و دستور کاری نیست که با دنبال کردن آن به نتیجه مورد نظر رسید بلکه عبارت است از مجموعه ای از ایده ها که به ویژگی های زمین شناسی منطقه توجه ویژه ای دارد. این روش در نتیجه تجربیات متعدد در کار تونلزنی به دست آمده است و برای به دست آوردن هر یک از این ایده ها و نیز جمعبندی آنها به عنوان یک روش سالهای زیادی وقت صرف شده است. نوآوری اساسی این ایده، یک فن ساختمانی یا یک روش خاص محاسباتی نمی باشد، اما برای ساختمان تونل در توده سنگ و چگونگی برخورد با آن ارائه طریق می نماید.
یکی از اصول موفقیت زای این روش گردآوری موضوعات متعدد از مهندسی عمران و مکانیک سنگ می باشد که شامل موضوعات نظری و عملی است.
روش اجرای ناتم:
با اینکه هنوز هیچ پشتوانه نظری حقیقی برای ناتم وجود ندارد اما عواملی وجود دارند که منجر به موفقیت این روش می گردند که عبارتند از:
1- بتن پاشی به عنوان سازنده سازه ترکیبی قوس سنگ که به حلقه حمال سنگ موسوم بوده و حفره را احاطه می کند.
2- بتن پاشی به مراتب قدیمی تر از ناتم می باشد اما ویژگی های عالی آن از نظر مقاومت و لغزش، این روش را به عنوان یکی از ابزارهای غالب نگهداری در تونلسازی به روش ناتم گردانیده است. بیشترین اهمیت آن امکان اجرای سریع برای پوشانیدن سطح تازه حفاری شده سنگ می باشد. مزیت دیگر آن دستیابی به یک مقاومت نسبی بالادر مدت زمان کوتاه، حدود 5 نیوتن بر میلی مترمربع (مگاپاسکال) در 6 ساعت می باشد.
شاتکریت در تونلسازی دارای اثر مضاعف است: محافظت سنگ در اثر هوازدگی و فرسایش: با بستن ترک ها تمرکز تنش در اطراف تونل کاهش یافته، همچنین ضخامت زیاد شاتکریت به عنوان یک قوس نگهدارنده عمل می کند. در تمام موارد اتصال اتصال تنگاتنگ با سنگ مهم می باشد. زیرا این عمل موجب می گردد سنگ بارها را مشترک حمل نموده و ساختاری مرکب با سنگ تشکیل دهد. شاتکریت مناسب، نیاز به یک تکیه گاه نیمه صلب را برآورده می سازد، زیرا دگرشکلی شعاعی زیادی را بدون شکستگی امکان پذیر می سازد. با دگرشکلی های بزرگ تونل، شاتکریت می شکند. اما در صورت مسلح شدن به توری سیمی یا رشته های فولادی، قطعات برش یافته شاتکریت خطری آنی برای خدمه ایجاد نخواهد کرد.
3- وسیله دیگر برای ساختن طاق بیرونی، قابهای فولادی می باشد. این قابها در توده های سنگ فشرده شده و بسیار خردشونده به کار گرفته شده و تکیه گاهی سریع و موثر برای سنگ به شمار می ایند. در چند سال اخیر کاربرد قوسهای پروفیلی به میزان زیاد افزایش یافته است. این قوس ها نسبت به قابهای فولادی مزایای بیشتری دارند و نیز به دلیل سبک وزن بودن، نصب آنها آسانتر می باشد.
4- در تونلسازی هوراه با مفاهیم ناتم، نصب میل مهارها جایگاه ویژه ای دارد و اهمیت آنها به همان اندازه اهمیت شاتکریت می باشد. این میل ها نیز مثل شاتکریت در صورت نصب موجب تشکیل حلقه حمال در اطراف توده سنگ می گردند. میل مهارها در برابر دگرشکلی شعاعی مقاومت کرده از اینرو ایجاد دگرشکلی کنترل شده می نماید که شکل ژئومتریک تونل را حفظ می نماید. همچنین میل مهارها از آنرو که تاثیر ناهمسانی و ناهمگونی را کاهش می دهند، تشکیل صفحات برشی و لغزشی را مشکل تر ساخته و سبب ایجاد مقاومت ماندگار بالا حتی در توده های سنگ به شدت دستخورده می گردد که این نیز به نوبه خود سبب بهسازی کیفیت سنگ می گردد. تنش مماسی در حلقه سنگ حمال موجب افزایش چسبندگی مهاری ها می گردد. طاقهای ثانویه ایجاد شده بین تکیه گاهها، در برابر تمایل توده سنگ نسبت به جابجایی به داخل تونل مقاومت ایجاد می نماید که این مقاومت به نزدیکی مهاری ها بستگی دارد. در صورتیکه طاق تونل تحت تنش زیاد در اثر فرایندهای تجدید آرایش دوباره قرار گیرد، یا اگر سیستم سنگ در معرض شکستگی قرار داشته باشد، تونل نیاز به بهسازی با بتن پاشی به سطح خواهد داشت.
بنابراین به طور خلاصه مواد پایدار کننده در ناتم عبارتست از: شاتکریت، میل مهارها، قوس های فولادی یا پروفیلی، صفحات فولادی و....
نتیجتا هدف اصلی ناتم ایجاد یک قوس نیمه صلب خارجی بلافاصله پس از حفاری با وسایل نگهداری از قبیل شاتکریت، کوه پیچ و غیره می باشد. این امر موجب تنظیم تنش در محدوده اطراف تونل گردیده از سست شدگی مخرب جلوگیری به عمل می آورد و این همان چیزی است که ناتم را از روش های تونلزنی محافظه کارانه تمیز می دهد. زیرا اصولا در شیوه های سنتی تونلسازی، بار سنگ می بایست تماما بوسیله تجهیزات نگهداری تحمل شود که این کار نیز مستلزم صرف هزینه های زیاد می باشد.
روش ناتم بیشتر در نتیجه تجربه عملی بوجود آمده و مانند دیگر روشهایی که در حال تکمیل و تکوین می باشند، دستخوش تغییر و تحولات و مشکلات متعددی گردیده تا به شکل کنونی در آمده است. این روش از انعطاف پذیری قابل توجهی در شرایط مواجهه با وضعیت های متفاوت توده سنگی برخوردار است.
بطور کلی ضروری می باشد که مطالعات و بررسی دقیقی به منظور بررسی ظرایط زمین ساختاری بویژه در زمیسن های نامناسب انجام گرفته، بین هزینه های مطالعات و اجرای عملیات رابطه ای منطقی ایجاد گردد.
تهیه مواد و مصالح مورد نیاز ناتم و طریقه ریختن بتن در فضاها، حتی در طرح های کوچک تونلسازی با ناتم نیاز به ساماندهی مناسب و کارآمد دارد که خود ناشی از تجربه ومهارت بالای معدنچی ها و اجراکاران دارد. اهمیت نصب شعاعی مهاریها به طور سیستماتیک در سنگ های سست، به منظور تامین توزیع مناسب تنش های بوجود آمده در قوس های دایره ای شکل سنگی، فوق العاده مناسب تشخیص داده شده است.
موفقیت در روش ناتم نیاز به آموزش های تئوریک و عملی همزمان در محل عملیات دارد زیرا تنها در ارتباط بودن نزدیک و دقیق مهندسان با مسائل و مشکلات در محل کار می تواند آنها را به اعمال راهنمایی های خاص و دقیق قادر سازد. یک بخش مهم و جدایی ناپذیر در این روش مشاهده رفتار تنش کرنش سنگ با فنون اندازه گیری می باشد.
ادامه دارد...
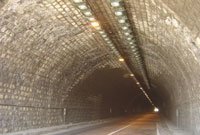
تونل سازی و روش های مختلف آن (2)
منبع : راسخون
اثر زلزله بر سازه های زیر زمینی و تونل مترو
برآورد خطر پذیری تونلها
برآورد خطر بر اساس HAZUS99:
در مجموعه HAZUS99 که توسط NIBS آمریکا تهیه گردیده، بصورت کامل آسیب پذیری سازههای مختلف در برابر زلزله مورد بررسی قرار گرفته است، این مجموعه بر اساس دادههای آمریکا تهیه شده و بصورت مجموعهای در 30 سی دی منتشر گردیده است.HAZUS99 دارای راهنمای کاملی است که فصل هفتم آن به شریانهای حیاتی اختصاص دارد. در بررسی آسیب پذیری شریانهای حیاتی، آنها را به هفت زیر مجموعه تقسیم مینماید که عبارتند از:
•بزرگراه
•راه آهن
•قطار برقی
•حمل و نقل اتوبوسی
•بندر
•حمل و نقل آبی
•فرودگاهها
در تقسیم بندی فوق، هرکدام از سیستم های حمل و نقل دارای اجزائی میباشند که تونل جزو اجزای بزرگراهها و سیستم راه آهن میباشد. لذا ما نیز بصورت جداگانه نقش تونل را در هر کدام از تقسیم بندیهای شریانهای حیاتی مورد بررسی قرار میدهیم.
تونل در سیستم بزرگراهی :
تونل یکی از اجزای سیستم بزرگراهی میباشد که به همراه سیستم راه و پلهای بزرگراهی، مجموعه بزرگراهها را تشکیل میدهد. از میان اجزای مختلف سیستم بزرگراهی ما فقط به بررسی آسیب پذیری تونلها میپردازیم.
1-داده های ورودی مورد نیاز
•مکان ژئوفیزیکی تونلها (طول و عرض)
•حداکثر شتاب زمین و حداکثر جابجائی زمین (PGD , PGA) در محل تونل.
•کلاس بندی تونل
2-تونلها در بحث آسیب پذیری بر اساس نحوه ساخت کلاس بندی میشوند:
•تونل حفاری شده (سوراخ شده)
•تونل خاکبرداری شده
3-تعاریف مربوط به سطح آسیب به تونلها
•Ds1 : بدون آسیب
•Ds2 : آسیب جزئی
آسیب جزئی به تونلها شامل ترکهای جزئی در پوشش تونل ( خرابی فقط نیاز به یک تعمیر سطحی داشته باشد) و افتادن چند سنگ و یا نشست جزئی در زمین در ورودی تونل
•Ds3 : خرابی متوسط
بصورت ترکهای متوسط در پوشش و فروریزش سنگ تعریف میشود.
•Ds4 : خرابی گسترده
بصورت نشستهای جدی در یک ورودی تونل و ترکهای گسترده در پوشش تونل
•Ds5 : خرابی کلی
ترکهای جدی در پوشش تونل که ممکن است شامل ریزش احتمالی باشد.
4-منحنی های تعمیرات اجزا
بر اساس تعداد روزهای مورد نیاز برای تعمیر خرابی های حاصل از زلزله پارامترهایی تعریف گردیده که برای تونل بصورت جداول و شکل زیر میباشد.
جدول توابع بازسازی پیوسته برای اجزای بزرگراهی
جدول توابع بازسازی منقطع برای اجزای بزرگراهی
5-توابع خرابی تونلها:
خرابی تونلها بر اساس خرابی زیر اجزای آن میباشد که عبارتست از پوشش و ورودی تونل (G&E 1994).یافته های شرکت G&E بر اساس دادههای زلزله گزارش شده توسط دودینگ و همکارانش میباشد در سال 1978 و اون در سال 1981 میباشد. خرابی این زیر سازهها در جداول زیر ارائه شده است.
کلا 10 تابع خرابی برای تونلها بدست آمده است که چهار تابع برای PGA و شش تابع برای PGD میباشد. ( توجه شود که هر کلاس تونل بصورت جداگانه مورد بحث قرار گرفته است). مقادیر متوسط و انحراف معیار این توابع در جدول دیگری ارائه شده است.
جدول الگوریتم های خرابی برای تونلها (G&E 1994)
شکل منحنی های بازسازی برای تونلهای بزرگراهی
شکل منحنی خرابی در سطوح مختلف برای تونلهای حفاری شده بر اساس حداکثر شتاب زمین
شکل منحنی خرابی در سطوح مختلف برای تونلهای خاکبرداری شده بر اساس حداکثر شتاب زمین
شکل محنیی خرابی در سطوح مختلف برای همه انواع تونلها بر اساس جابجائی ماندگار زمین
تونل در سیستم راه آهن :
در مورد تونل در HAZUS99 تاکید زیادی نشده است و فقط عنوان شده که تونلهای راهآهن معمولا مانند پلها، باعث بند آمدن ترافیک و ... نمیشوند مگر اینکه کاملا عملکرد خود را از دست داده باشند.
بسیاری از تعاریف در تونلهای راهآهن دقیقا همان تعاریف تونلهای بزرگراهی میباشد، باید توجه نمود که ایستگاههای راه آهن شهری جزو اجزای این سیستم حمل و نقل میباشد قسمتهای مورد نیاز در اینجا بیان میشود.
در راهآهن نیز تونلها به دو نوع حفاری شده و خاکبرداری شده تقسیم میشوند. در مورد ایستگاههای شهری در این ایین نامه گفته شده است که ایستگاههای مترو در حکم اتصالات حیاتی سیستم هستند و از نظر عملکرد سیستم بسیار مهم میباشند. در آمریکای غربی، این تسهیلات معمولا به صورت دیوارهای برشی بتنی مسلح و یا قابهای خمشی ساخته میشوند در حالی که در آمریکای شرقی ایستگاههای کوچک اغلب چوبی هستند و ایستگاههای بزرگتر معمولا با مصالح بنایی و یا قاب فلزی مهاربندی شده هستند.
1-داده های ورودی مورد نیاز
•برای تونلهای راه آهن :
oهمانند تونلهای بزرگراهی
•برای ایستگاههای شهری :
oمکان جغرافیایی تسهیلات
oPGA و PGD در محل تسهیلات
oکلاس بندی تسهیلات
2-شکل توابع خرابی
توابع خرابی و یا منحنی های خرابی برای تمام اجزای راه آهن که در زیر توضیح داده شده است، بصورت تابع لوگ نرمال تعریف شده اند که احتمال رسیدن و یا گذشتن از سطوح خرابی مختلف برای یک سطح مشخص شده حرکت زمین میباشد. هر منحنی خرابی با یک مقدار میانگین از سطح حرکت زمین و مقدار انحراف معیار مشخص میشود. حرکت زمین با پارامتر بیشینه شتاب زمین (PGA) و خرابی زمین با پارامتر جابجائی ماندگار زمین (PGD)تعیین میشود.
•برای تونلها، منحنی های خرابی بر اساس PGA و PGD تعیین میشود.
•برای تسهیلات راهآهن مانند ایستگاههای شهری نیز PGA و PGD مشخص کننده هستند.
3-تعاریف مربوط به سطح آسیب
سطوح آسیب تونلها همانند تعاریف مربوط به تونلهای بزرگراهی میباشد. و در مورد ایستگاهها :
•Ds1 : بدون آسیب
•Ds2 : آسیب جزئی به سازه
•Ds3 : خرابی متوسط سازه
•Ds4 : خرابی گسترده
•Ds5 : آسیب کلی و خرابی گسترده
4-منحنی های تعمیرات اجزا
منحنی های بازسازی بصورت زیر میباشد.
جدول توابع بازسازی پیوسته برای اجزای راه آهن
جدول توابع بازسازی منقطع برای اجزای سیستم حمل نقل ریلی
شکل منحنی های بازسازی برای تونلهای راه آهن
اثر زلزله بر سازه های زیر زمینی و تونل مترو
تاثیر ارتعاشات زلزله بر تونلها:
آسیب پذیری سازههای زیر زمینی در برابر زلزله هم میتواند به واسطه گسیختگی زمین در هنگام وقوع زلزله و هم به دلیل ارتعاشات ناشی از زلزله روی دهد. گسیختگی زمین در هنگام وقوع زلزله عمدتا شامل گسلش، زمین لغزش و روانگرایی میباشد.
بحث مربوط به گسلش در فصل قبل بصورت جداگانه مورد بررسی قرارگرفت، ولی بجز گسلش، زمین لغزش و روانگرایی نیز از پدیدههای طبیعی ناشی از زلزله میباشد. زمین لغزش ها که معمولا توسط زلزله تحریک میگردند، بخصوص در ورودی-خروجی تونلها میتوانند صدمات زیادی را به فضاهای زیر زمینی وارد نمایند. بسیاری از گزارشات مربوط به آسیب فضاهای زیر زمینی در اثر زلزله، به واسطه ایجاد لغزش در مدخلهای تونلها بودهاند. روانگرایی نیز بخصوص چنانچه فضای زیر زمینی در رسوبات سست دارای درصد بالای ماسه و سیلت احداث شده باشد، میتواند صدمات زیادی را به فضای زیر زمینی وارد نماید. این آسیبها بیشتر در رابطه با تونلهای مترو در نواحی شهری که از رسوبات منفصل عبور میکنند دیده شده است.
گزارشی از یک پروژه تونلسازی در نوع خود بینظیر
پروژه تونل SMART (Stormwater Management and Road Tunnel) SMART
SMART درخشش مهندسی در اعماق زمین
تونل SMART اولین تونل دو منظوره جهان است که در شهر کوالالامپور پایتخت کشور مالزی ساخته شده است. ساخت این تونل از سال 2003 شروع و در ژوئن 2007 بهرهبرداری از آن آغاز شده است. این تونل ابتدا بهعنوان مسیری برای انحراف آبهای خروشان و سیلابهای رودخانهای که از بههم پیوستن دو رودخانه بزرگ در مرکز شهر حاصل شده است، در نظر گرفته شده بود. ولی سپس با یک ایده جالب و خلاق و با در نظرگرفتن قطر داخلی 8/11 متر، تونل به گونهای طراحی شد که بتواند در زمانهای غیراضطراری که جریان آب چندان قوی نیست بهعنوان تونلی رفت و آمدی (در دو طبقه) برای وسایل نقلیه جهت کمکردن بار ترافیکی یکی از شاهراههای مهم و شلوغ شهر مورد استفاده قرار بگیرد.
بهرهبرداری از این تونل در سه حالت میتواند انجام بگیرد:
حالت اول (حالت عادی یا نرمال): زمانی است که جریان آب رودخانه به قدری کم است که اساساً نیازی به انحراف توسط تونل ندارد.
حالت دوم: زمانی است که طوفانهای کوچک یا متوسط رخ میدهد ولی فشار جریان آب زیاد نیست. در چنین حالتی جریان آب به داخل تونل منحرف شده و از طریق مسیر فرعی به پایینترین قسمت تونل هدایت میشود. در این حالت دو مسیر عبور و مرور بالایی تونل همچنان بر روی وسایل نقلیه باز است.
حالت سوم: حالتی است که در زمان طوفانهای سهمگین رخ میدهد. در چنین حالتی کل تونل بر روی وسایل نقلیه بسته میشود و پس از اطمینان از خارجشدن کلیه ماشینها (بهوسیله تعداد زیادی ایستگاههای رفتارسنجی تا زمانی که یک وسیله نقلیه در داخل تونل باشد درهای ورودی آب باز نمیگردد) جریان سیلاب بهطور خودکار به داخل تونل هدایت میشود. ظرفیت آب در تونل در چنین حالتی به سه میلیون مترمکعب میرسد.
• روش ساخت تونل
شهر کوالالامپور از نظر زمینشناسی بر بستری از آهک قرار گرفته است. ضمناً این شهر از سطح دریا نیز بالاتر است. از مشخصههای اصلی این لایههای آهکی وجود تختهسنگها، گودالها و باتلاقهای متفاوت است. با توجه به طبیعت زمینشناسی شهر بیشتر ایدههای طراحی و اجرا به سمت و سویی میل کرده است که کمترین اثر منفی را بر روی شرایط محیطی و زمینشناسی شهر وارد نماید.
لذا برای این پروژه از ماشین TBM مدل Slurry Shield استفاده شده است که به هنگام کار در برخورد با بسترهای آهکی و مواجهه با آبهای زیرزمینی و صخرههای سخت مقاومت خوبی از خود نشان میدهد. وجود یک سپر مقاوم که با فشار هوا کار میکند امکان آن را فراهم میسازد که ماشین در مواجهه با آبهای زیرزمینی و خاکهای سست تعادل خود را کاملاً حفظ نماید.
• ایمنی تونل
از نظر استاندارد های امنیتی و ایمنی نیز اسمارت از وضعیت خیلی خوبی برخوردار است. خروجیهای اضطراری فراوان، سازه ضد زلزله، صدها دوربین و وجود مرکز کنترل که شبانهروز تردد خودروها و عبور جریان آب را زیر نظر دارند اسمارت را در این زمینه نیز بی همتا کرده است. تونل SMART دارای دستگاههای تهویه ویژهای است که در هر کیلومتر از تونل تعبیه شده است. این دستگاههای قوی تهویه بهطور دائم هوای آلوده تونل را خارج مینماید
منابع:
مجله بلور (دانشکده معدن و متالوژی دانشگاه تهران)
وفائیان.م. بررسی پیشرفت مبانی طرح سابرت و اجرای تونل، مجموعه سخنرانی های سومین سمینار توونلسازی. خرداد 1366
انصاری، ع. مطالب ارائه شده در جزوه درسی.
طاهری، ع. مطالب ارائه شده در جزوه درسی.
کدیور، م.ح. طراحی تونل بوسیله ناتم از دیدگاه مطالعات آماری
سایت جامع علمی داکفا ( www.docfa.ir )
http://geoaria.blogfa.com
http://docfa.ir
http://www.gsinet.ir
http://forum.parsigold.com

انواع سیمان ها
منبع : راسخون
سیمان ها بر اساس ترکیب و فازهای تشکیل دهنده به انواع مختلفی تقسیم بندی می شوند .عموماً در همه ی کشورها استانداردهایی برای سیمان به عنوان یک ماده پایه جهت تولید انواع ملاتها و بتن تدوین گردیده است .تفاوت های موجود در رابطه با توسعه ی اقتصادی و صنعتی ،منابع مواد خام و شرایط اقلیمی منجر به توسعه ی مصالح ساختمانی و روشهای گوناگون ساختار در کشورهای مختلف گردیده اند که این امر خود منجر به تولید مختلف سیمان شده است .بدین دلیل تفاوتهایی اساسی نیز بین استانداردهای کشورهای مختلف در مورد سیمان وجود دارد .که همگام با سایر موارد بر مشخصات دوام بتنهای ساخته شده از این سیمانها تأثیر گذار هستند.
در اروپا کار بر روی تدوین اصولی فنی استاندارد سیمان اروپایی از سال 1975در حال توسعه و پیشرفت بوده است.در این راه،تاکید اولیه بر روی مجموعه روش های مورد توافق در انجام آزمایشات بود که این روشها در [D42]EN196ارائه گردیده اند .بدین ترتیب مشخصات انواع بتن ،ترکیبات و کلاس مقاومتی آنها که مورد پذیرش کلیه کشورهای اروپایی بود در [E26] EN1971:2000مشخص گردید .مبنای این استاندارد سیمانهایی با سخت شدگی سیلیکات کلسیم بودند که در کشورهای مرکزی و غربی اروپا برای مصارف عمومی[A19] تولید می گردیدند. با خواص ویژه اضافی (سیمانهای ویژه (special cement)و سیمانهای با مکانیزم های متفاوت سخت شوندگی در بخشهای دیگر این استاندارد می بایست مورد توجه قرار گیرد.[E26،s193].از نوع سیمان مشخص شده در EN197-1در ابتدا فقط 12 نوع سیمان در استاندارد سیمان آلمان [oct.1994 [D51 )
DIN1164مورد پذیرش قرار گرفتند .علت پذیرش این 12 نوع سیمان در آیین نامه ی DIN1164.اثبات نقش موفقیت آمیز آنها در دوام بتن های ساخته شده از این نوع سیمانها بود.از تاریخ اول آوریل 2001 استاندارد سیمان اروپا به عنوان (Feb.2001)DIN EN1971-1:2001به عنوان استاندارد سیمان آلمان پذیرفته شده که بدین ترتیب این استاندارد جایگزین (OCT 1994)DIN 1164-1 می گردد.استفاده از سیمانهای مشخص شده در استاندارد جدید DIN EN197-1مشمول مقررات آیین نامه های 1-DIN 1045-2 (D44،49،w2)وDIN.EN 206می گردد.
در این میان استانداردهای ASTMنیز از اهمیت خاصی برخوردارند .این استانداردها بوسیله ی انجمن استاندارد آمریکا انتشار یافته است برای اطلاع بیشتر خواننده ضوابط مربوط به این سیمانها را با شماره ی ASTMآنها معرفی می کنیم:
-سیمان پرتلند که در [A46]ASTM C150مشخص شده اند
-سیمان هیدرولیکی مخلوط با ترکیبات مشخص که در ASTMc595m[A60]تعریف شده است .
-سیمان هیدرولیکی مخلوط با ویژگی های اجرایی مشخص که در [A66]ASTMc1157mمشخصات آنها ذکر شده است و مطابق با اصطلاحات استاندارد شده مربوط به سیمان در ASTM c845[A49، مورد بحث قرار گرفته است.
مطابق با اصطلاحات استاندارد شده مربوط به سیمان در A49 ASTMC، سیمان هیدرولیکی مخلوط (Blended Hydraulic Coment) سیمانی است که از دو یا چند ماده غیر آلی تشکیل شده که حداقل یکی از آنها سیمان پرتلند و یا کلینکر سیمان پرتلند نیست و از آمیختن مواد با یکدیگر به طور همزمان در حین آسیاب کردن و یا آسیاب کردن آنها به طور مجزا و سپس مخلوط کردن آنها با هم تولید می شود .بنابراین به جای واژه سیمان هیدرولیکی مخلوط بهتر است عنوان صحیح سیمان ساخته شده از چند جزء اصلی را به کار برد.
البته همانگونه که اشاره شد در هر کشور استاندارد معینی وجود دارد و سیمان جزء موادی است که دارای استاندارد اجباری است.از این رو توجه به اهداف استفاده از سیمان در انتخاب نوع آن ضروری است. نوع سیمان مصرفی بر روی خواص گیرش،استحکام و...موثر است،لذا باید در انتخاب نوع سیمان دقت کنیم .با مراجعه به استانداردهای مختلف موجود در سطح کشور و همچنین سطح جهان می توانیم افزودنی های مورد نیاز برای سیمان های ویژه را انتخاب کنیم.در زیر سیمان های متداول مصرفی در کشور را مورد بررسی قرار دادیم.لازم به توضیح است که توجه به افزودنی های مصرفی در سیمان بسیار ضروری می باشد.(این افزودنی ها ممکن است به مواد اولیه ،به خوراک کوره و یا به کلینکر اضافه شوند.)
سیمان پرتلند نوع I
این نوع سیمان که یک سیمان پرتلند معمولی است در مواردی مصرف می شود که هیچگونه خواص ویژه ای مانند سایر انواع سیمان مورد نظر نباشد.
سیمان پرتلند نوعII
این سیمان برای استفاده های عمومی استفاده می شود.این سیمان گرمای هیدراسیون متوسط دارد و در کاربردهایی که گرمای هیدراسیون متوسط مد نظر باشد مطلوب است.
سیمان پرتلند نوعIII
این نوع سیمان ایجاد مقاومت بالا در کوتاه مدت می کند .مثلاً در مکان هایی که بخواهیم پایه های موقت برای پل ها ایجاد کنیم می توانیم از این سیمان استفاده کنیم.در این پایه های موقت که مدتی کوتاه برای ما مفید هستند مقاومت بالا در کوتاه مدت مورد نظر است.
سیمان پرتلند نوعV(نوع پنج)
این نوع سیمان در مواقعی که نیاز به مقاومت زیاد در مقابل سولفاتها مورد نظر باشد ،استفاده می شود.ترکیب این نوع سیمان ها با توجه به استاندارد متغیر است ولی اکثراً دارای ترازهای پایین تری کلسیم ،آلومینات هستند .ضمناً سیمان های روباره ای حاوی ترازهای بالای روباره ی کوره ی آهن گدازی نیز از جمله سیمانهای با مقاومت بالا در برابر سولفات شناخته می شوند.
سیمان بنایی
مورد استفاده ی این نوع سیمان در مکان هایی است که به مقاومتهای کمتر از سیمان پرتلند نوع Iمورد نیاز باشد.
ملاتها و اندودهای بنایی معمولاً ازچسباننده هایی تولید می شود که موجب بهبود کارایی و ظرفیت نگهداری آب ملات تازه شده،اما توسعه مقاومت آنها تا به حدی کمتر از سیمان محدود کننده،تا بدین ترتیب ملات سخت شده باز هم دارای تغییر شکل پذیری کافی باشد.
این چسباننده عموماً از سیمان ،روباره دانه شده کوره آهن گدازی ،پوزولان و احتمالاً آهک هیدراته یا آهک هیدرولیکی و پر کننده(Filler)تشکیل می شوند.
سیمان سفید
این نوع سیمان دارای رنگ سفیدی است و برای استفاده در سطح ساختمانها و مواقعی که استفاده از سیمانهای بدون زنگ با مقاومتهای بالا مورد نیاز باشد،از این سیمان در تولید انواع سیمانهای رنگی استفاده می شود.
سیمان پرتلند -آهکی
این نوع سیمان در تهیه ی ملات بتن در کلیه ی مواردی که سیمان پرتلند نوع Iبه کار می رود قابل استفاده است.دوام بتن را در برابر یخ زدن،آب شدن و املاح یخزا و عوامل شیمیایی بهبود می دهد.
سیمان پرتلند -پوزولانی
در ساختمانهای بتنی معمولی و بیشتر در مواردی که مقاومت متوسط در مقابل سولفاتها و حرارت هیدراتاسیون متوسط مورد نظر باشد،استفاده می گردد.
سیمان سرباره ای ضد سولفات
در مواقعی که مقاومت متوسط در برابر سولفاتها و حرارت هیدراتسیون متوسط مورد نظر است از این نوع سیمان استفاده می شود.
سیمان نسوز
این نوع سیمان ها از ترکیبات حاوی آلومین تشکیل شده اند .این سیمانها به سیمانهای آلومینی یا آلومینات کلسیمی معروف اند . این سیمان ها دارای گریدهای مختلفی هستند و به عنوان ماده نسوز و بادرصد خلوص بالا در صنایع حرارتی و اتمسفرهای Co،H2 به کار می روند.
سیمان پرتلند ضد آب
این سیمان به رنگ سفید،خاکستری تولید می شود، این نوع سیمان انتقال مویینه آب تحت فشار ناچیز یا بدون فشار،کاهش می دهد و لی جلوی انتقال بخار آب را نمی گیرد.
سیمان های چاه نفت
این سیمانها برای درزگیری چاه های نفت به کار می رود ،عمده این نوع سیمانها دیرگیر بوده و در برابر دما ها و فشارهای بالا مقاوم می باشند ،این سیمان ممکن است در حفره های چاه های آب و فاضلاب نیز مصرف می شوند.
سیمانهای باگیرش تنظیم شده
سیمانهای باگیرش تنظیم شده به گونه ای کنترل و ساخته می شود که می تواند بتنی با زمانهای گیرش از چند دقیقه تا یک ساعت تولید کند.
سیمان های رنگی
این سیمانها بیشتر جنبه ی تزئینی و آرایشی دارند و در نما سازی سیمانی و تولید بتن نمادار به مصرف می رسند .
*استفاده از مطالب این مقاله با ذکر منبع « راسخون » بلا مانع است.
منبع :مرجع کامل تکنولوژی سیمان/میر مسعود معطر فرازی -تکنولوژی پخت سیمان /محمد رضا عزیزیان
advance tecnology in cement in dustry/michel Richman.

سیمان
منبع : راسخون
مقدمه:
مصرف سیمان درکشورها می تواند به عنوان شاخصی از پیشرفتگی آنها در نظر گرفته شود. البته توجه به اقلیم هر کشور،نوع مصارف سیمان و مسائلی دیگر ضروری می باشد. در کشورها نیز درطی چند سال گذشته نیاز به این ماده ی پر اهمیت مهندسی بیشتر شده است و این نیاز منجر به تأسیس کارخانجات متعددی در سطح کشور شده است. البته از دیدگاهی دیگر کشور ایران به خاطر دارا بودن منابع عظیم نفت و انرژی و دارا بودن ذخایر مواد اولیه ی مصرفی در بخش سیمان،مستعد تولید سیمان نیز می باشد. اقلیم بیابانی و نیمه خشک منطقه ی ما و عدم وجود منابع چوب نیز می تواند عاملی دیگربرای توسعه ی صنعت سیمان و مصرف آن در بخش ساختمان سازی باشد.
سیمان یک ماده ی متداول در کشور ما محسوب می گردد و کسی نیست که این ماده را نشناسد ولی اطلاعات افراد در مورد این ماده اندک است از این رو،دراین مقاله تلاش شده است تا اطلاعاتی مناسب در مورد صنعت سیمان ارائه گردد. همچنین مطالب به نحوه ای بیان شده است تا عموم عزیزان بتوانند از آن استفاده کنند. امیدواریم که مطالعه ی این مقاله باعث افزایش سطح اطلاعات خواننده باشد.
1. تعریف:
سیمان پودری است که خاصیت چسبانندگی ایجاد می کند. این ماده پس از واکنش با آب می تواند ایجاد ساختارهای بلوری یا هیدراتهای بلند کند که پس از سخت شدن،حتی در زیر آب هم به صورت یک بافت سخت و یکپارچه در می آید.
بنابر یک تعریف درگی سیمان گردی است نرم، جاذب آب و چسباننده خرده سنگ که اساساً مرکب است از ترکیبات پخته شده و گداخته شده ی اکسید کلسیم با اکسید سیلسیم، اکسید آلومینیم و اکسید آهن. ملات این گرد قادر است به مرور در مجاورت هوا و یا در زیر آب سخت شود،در زیر آب ضمن داشتن ثبات حجم مقاومت خود را نیز حفظ می نماید. و در فاصله ی 28 روز در زیر آب ماندن دارای حداقل مقاومت 250 کیلوگرم بر سانتیمتر مربع می شود.
در رم قدیم مخلوطی از خرده سنگ و آهک پخته درست می کردند که از ترکیب این مخلوط با آب،بتن حاصل می شد و از این بتن برای کارهای ساختمانی استفاده می گردید. این نوع ساختمانها را (caementitium) opus می نامیدند. به مرورکلمه ی cementum به مخلوط های مورد استفاده در این نوع ساختمان سازی اطلاق گردید. منظور از cementum نوع خاصی خرده سنگ است که وقتی پودر آنها با آهک مخلوط می شد،مخلوط حاصله دارای خاصیت هیدرولیکی بیشتر می شد و به مرور در مجاورت هوا و در زیر آب سخت می گردید و دارای مقاومت و سختی قابل توجهی می شد. این خرده سنگها از باقیمانده ی آتشفشان یعنی خاکستر آتشفشان بودند و یا اینکه از خردکردن خرده آجرهای تولید شده درکوره آجرپزی که در واقع همان خاک رس پخته است،بدست می آمده اند.
2. تاریخچه
همانگونه که گفتیم مواد چسباننده ی پایه هیدرولیکی به دوران رومیان باز می گردد. در آن دوران رومیان از موادی شبیه به سیمان امروزی استفاده می کردند. این مواد که جزء مصالح ساختمانی آن دوره بودند از ترکیب خرده سنگ با یک ماده ی چسباننده مانند آهک پخته ساخته می شدند. علاوه بر این مواد، افزودنی هایی شبیه پودر بسیار نرم سفالهای پخته شده و خاکستر آتشفشانی نیز اضافه می شده است. مواد افزودنی باعث ایجاد خاصیت چسبندگی هیدرولیکی در مخلوط می شود. این ماده ی چسباننده در سیر تحول به نام سیمان (cement) معروف گشت. درطول تاریخ این ماده ی چسبنده ابتدا cementum و بعدها با نام های cament, cimentum و نهایتاً سیمان (cement) نام گرفت.
در سیرتحول ساخت سیمان،اهمیت خاک رس در ترکیب مواد اولیه ی دانسته شد. و با توجه به نیاز،سیمان های با کاربردهای خاص و ویژه تولید شد. با توجه به اینکه مسائل مربوط به سیر تحولات تاریخی سیمان گسترده است، آنها را بیان نمی کنیم و به سراغ سیر تحول ادوات مورد استفاده در صنعت سیمان می رویم:
1. 2. سیر تحول روش های تولید
در تولید سیمان کلاً دو روش وجود دارد که به شرح زیر است:
1) روش تر
2) روش خشک
در روش تر مواد اولیه به صورت دوغاب درآمده و دوغاب حاصل پس از آسیاب شدن و رسیدن به خواص مطلوب به داخل کوره ای می روند که در این کوره ابتدا آب دوغاب خشک شده،سپس واکنش های مربوط به زنیترینگ انجام می شود. البته لازم به توضیح است که در فرآیند تر معمولاً مواد خردایش یافته در تانکرهایی آب خور شده و کلاً خواص دوغاب پیش از مرحله ی پخت معین می گردد.
در روش خشک مواد پس از خردایش و آسیاب ابتدا پیشگرم شده،سپس به داخل کوره رفته که طول کوره ی پخت کلینکر در این روش معمولاً بسیارکوتاه تر از حالت تر می باشد. علت این کوتاهی این است که در روش خشک نیاز به خشک کردن مواد خردایش یافته نیست.
توضیحات داده شده دربالا توضیحات مختصری در مورد فرآیند تولید سیمان بود. در قسمت های بعدی در مورد فرآیند تولید سیمان به صورت جزئی تر صحبت می کنیم.
2. 2. سیر تحول کوره ی پخت کلینکر
کوره های استوانه ای عمودی (shaft kiln) که به صورت تناوبی کار می کردند اولین تجهیزات مورد استفاده در فرآیند پخت سیمان محسوب می شدند. اولین قدم در راه تولید پیوسته سیمان با به کارگیری کوره ی حلقوی هافمن (Hoffmann Annular Kiln) برداشته شد. واژه کلینکر سیمان نیز در این زمان یعنی هنگامی متداول گردید که تغذیه ی کوره های حلقوی به وسیله مواد خامی صورت می پذیرفت که شکل قطعات آجر (خشت) در می آمدند و مشابه با پخت آجر در کوره های آجرپزی عمل پخت آنها صورت می گرفت. کوره های چرخنده پخت سیمان (Rotary Cement Kilns) به دوره ای باز می گردند که امتیازشان توسط فردریک رانسوم در سال های 1885/1886 به ثبت رسید. پخت آزمایشی سیمان در کوره های گردنده در آلمان از سال 1897 آغاز شد و تولید صنعتی کلینکر سیمان دو سال بعد آغاز گردید. اولین کوره ی دارای پیش گرمکن مشبک (preheater) در سال 1929 و اولین کوره دارای پیش گرمکن سیکلونی (cyclonepreheater) در سال 1950 وارد چرخه ی تولید سیمان درآلمان شدند.
3. 2. سیر تحول وسایل خردایش در کارخانجات سیمان
در گذشته سنگ شکنهای فکی (Jaw crushers) جهت خردکردن اولیه ی مواد خام و کلینکر،غلتکهای خردکنده (Grinding Rolls) برای ریزکردن مواد خام خردشده در مرحله اول و نهایتاً تجهیزات آسیاب سنگی (Millstone Arrangements) که از دو قطعه سنگ آسیاب با قطرهای 105- 0.8 متر واقع بر روی یکدیگر تشکیل می شد، جهت پودرکردن مواد خام مورد استفاده قرار می گرفتند. خوراک آسیاب از طریق بازشویی واقع در مرکز سنگ فوقانی به فضای بین سنگ ساکن فوقانی و سنگ متحرک تحتانی که توسط یک شفت محوری می چرخید به آسیاب وارد و خرد می گردید.
هدف اولیه توسعه ی روشهای آسیاب کردن بر محور تولید پودرهای نرم تر و بالا بردن توان عملیاتی تجهیزات متمرکز بود. مطابق با استاندارهای موجود نرمی سیمان باید به اندازه ای می بود که درحین الک کردن با الکی با چشمه هایی به قطر 0.2 میلی متر، مقدار باقیمانده ی روی الک از حداکثر 20% کمتر باشد. این امر موجب شد تا تجهیزات آسیاب با تجهیزات سردکننده که ازجمله معایب آنها استهلاک بیش از حد و بازده پایین آنها بود،تواماً به کار گرفته شد که در این راه ظهور سیستم های جداکننده ی مکانیکی عمل کننده به کمک هوا در سال 1889 پیشرفت مهمی محسوب می شد .
از جمله تجهیزاتی که بعدها جهت آسیاب کردن مواد مورد استفاده قرار گرفتند می توان به آسیاب های لبه ای (Edge Mill)، که برای آسیاب کردن مواد خام درحالت تر به کار می رفت،انواع مختلف آسیاب گلوله ای (Ball Mill) و آسیاب گریفین (Griffinmill) که در آمریکا طراحی شده بود، اشاره کرد. در آسیاب نوع گریفین آونگی وجود داشت که سر آن به شکل یک غلتک خردکننده طراحی شده بود و در طول رینگی فولادی می چرخید که در این حالت عمل آسیاب کردن با نیروی گریز از مرکز ناشی از چرخش آونگ انجام می شد.
دستیابی به پودرهای نرم تر با توان عملیاتی قابل قبول در واقع با استفاده از آسیاب لوله ای (tube mill) در صنعت سیمان آلمان و در سال 1892 ممکن گردید. آسیابهای لوله ای اولیه آسیابهای تک محفظه ای (mill single chamber) بودند که قطرآنها 102 متر و طول آنها بین 6-5 متر و ظرفیت تولید آنها بالغ بر3 تن سیمان در ساعت بود. سیمان خروجی از این نوع آسیاب از چنان نرمی برخوردار بود که پس از الک کردن آن با الک به قطر 0.09 میلی متر مقدار باقیمانده بر روی آن در حدود 15 درصد می شد. ضمن این که توان برق مصرفی آنها نیز حدوداً 20 کیلو وات ساعت بر واحد زمان [kwh A] بود. از سال 1920 انواع مختلف آسیابهای لوله ای جایگزین سایر آسیابها جهت آسیاب کردن مواد خام و سیمان گردیدند.
3. مواد اولیه در تولید سیمان
مواد اولیه سیمان از ترکیبات مختلفی مانند کربنات ها، آلومینا سیلیکات ها،اکسید آهن و آلومینیوم تشکیل می شود. البته سه جزء کربنات ها،آلومیناسیلیکات ها و اکسید آهن در تشکیل کلینکر ازاهمیت خاصی برخوردارند. البته اجزای دیگری هم به مواد اولیه اضافه می شود که این مواد اضافه شده نقش تسهیل کننده را بر عهده دارند. این مواد بر روی شرایط کوره، پیش گرم کن و شرایط پخت تأثیر می گذارند.
مهمترین مواد اولیه مورد استفاده در صنعت سیمان ترکیبات آهک است. مواد آهکی که در صنعت سیمان استفاده می شود مینرالهای حاوی کربنات کلسیم است که در بین این مینرالها سنگ آهک مهمترین نوع مینرال است که در صنعت سیمان استفاده می شود. و علاوه بر آن مواد آهکی مثل سنگ گچ، مارل، مواد آهکی و شنهای دریایی و سنگهای مرمریتی نیز استفاده می شود. که این سنگ های از نظر ترکیب شیمیایی از کربنات کلسیم تشکیل شده است. و شکل این مینرال ها کلسیت و آرگونیت حاوی مقادیر متفاوتی ناخالصی از جمله کوارتز یا سیلیس، خاک رس، فسفات، پریت (Fe S2)، ستریت (Fe CO3)، ژئوتیت (Fe oH)، رونومیت 2(CaMg (CO3، مگنیت، گچ (CaSo4. 2H2o)، فلوریت (CaF2) و... می باشد.
سنگی آهک در کاخانه های سیمان بر مبنای منشأ تشکیل و انواع ناخالصی های موجود درآن طبقه بندی می شود. چون منشأ تشکیل سنگ بر روی مینرالهای موجود، درجه ی بلور شدن،اندازه ذرات، قدرت سیمانی شدن، میزان فشردگی و ناخالصی های موجود در سنگ تأثیر داشته و همچنین تأثیرات عمده ای روی خواص فیزیکومکانکی، میزان تجزیه پذیری، قدرت ترکیب سنگ با سایراجزای سیمان، دارد. که این خواص از اهمیت خاصی بر روی فعالیت، واکنش پذیری و میزان ترکیب پذیری ماده اولیه، درجه خردشوندگی و همچنین تأثیرات آن روی آسیابهای سیمان دارد.
آسیاب نشدن کامل مواد اولیه موجب واکشن ناقص اجزا شده که این مسأله باعث تخریب بتن به خاطر تشکیل و وجود مواد ناخاسته در بتن می گردد.
1. 3. مواد افزودنی، مواد تسهیل کننده ی ترکیبات مورد استفاده در کارخانجات سیمان
این مواد عبارت اند از: سنگ معدن های طبیعی و یا زباله های صنعتی که برای تصفیه ترکیبات موجود برای تولید انواع سیمان مورد استفاده قرار می گیرد. افزایش این مواد به سیمان چه قبل از ورود مواد اولیه به کوره،و چه بعد از تشکیل کلینکر و درحین آسیاب شدن به سیمان،می تواند تأثیرات متفاوتی در خواص بعدی سیمان داشته باشد. از جمله ی این مواد عبارت اند از:ترکیبات آلومینیوم سیلیکات که در سنگ معدنهای مختلف درصد سیلیس و با آلومین متفاوت است. از جمله سنگهای غنی از سیلیس مثل ماسه سنگ، فلینت، دیاتومیت و سنگهای کوارتریتی و همچنین سنگهای آلومینا سیلیکاتی (خاک رس، شیل و...) است که درصد تخلخل سنگ ها متفاوت است که دو نوع اول از نوع سنگهای نرم می باشد و شیل از نوع سنگهای رسوبی می باشد. در این سنگها علاوه بر ترکیبات آلومینا سیلیکات ترکیبات دیگری از جمله سیلیس آزاد، منیزیت، قلیایی ها و گوگرد نیز وجود دارد.
برای تولید سیمان سفید از افزودنی کائولن سفید با درصد آلومینای بالا استفاده می شود.
بوکسیت یکی از انواع رسهاست که ترکیب شیمیایی آن دارای مقادیرمتفاوتی هیدروکسید آلومینیوم است و همچنین مقادیر متفاوتی مینرالهای مختلف هیدراته ی آهن وجود دارد در صورتی که سنگ غنی ازآلومینیوم باشد مینرالهای موجود در آن را بوهمیتا (Al2O3. 3H2O - لا) و یا دیاسپور (Al2O3. H2O-×) و گپسیت (Al2O3. 3H2O) تشکیل می دهد. که در تولید سیمان استفاده می شود به عنوان مواد تسهیل کننده ترکیبات از سنگ معدنهای غنی از اورانیوم استفاده می گردد.
میزان استفاده از ترکیبات آلومینایی بین 5-10 درصد در کارخانه سیمان متغیراست و در صورتی که ازسنگ آهک خالص استفاده شود این مقدار تا 25 درصد می تواند افزایش یابد. علاوه براین ترکیبات مواد دیگری هم استفاده می شود که عبارت است از: خاکستر آتش فشانی، باقی مانده سوختهای زغال سنگ در نیروگاه ها،سرباره ذوب آهن و ضایعات کارخانه کاغذسازی.
علاوه بر ترکیبات شیمیایی که لازم است با هم، هم خوانی داشته باشند، مواد افزودنی و مواد تسهیل کننده نیز باید با هم، هم خوانی داشته باشند.
4. فرآیند تولید سیمان
1. 4. خردایش مواد خام
معمولاً خردایش مواد اولیه توسط ماشینهای مختلف صورت می گیرد. که در این قسمت سنگ شکن ها و آسیاب ها قرار گرفته اند.
سنگ شکنهای مورد استفاده در صنعت سیمان عبارتند از:
1) سنگ شکن فکی
2) سنگ شکن مخروطی
3) سنگ شکن نوردی
مکانیزم سنگ شکن های بالا براساس اعمال فشار بر روی مواد اولیه است. که علاوه براین نوع سنگ شکن ها سنگ شکن هایی وجود دارند که اساس کارآنها ضربه است. این نوع سنگ شکن ها عبارتند از:
1) سنگ شکن ضربه ای
2) سنگ شکن چکشی
از لحاظ بازده،بازده سنگ شکن چکشی از سه نوع فکی، مخروطی و نوردی بیشتر است. امروزه نیز به خاطر همین مسئله استفاده از این نوع سنگ شکن در کارخانجات سیمان متداول گشته است. این نوع سنگ شکن بسیارعظیم الجثه است. و دارای چکش های بسیار بزرگ است.
آسیاب های مورد استفاده در کارخانجات سیمان دو نوع اند:
1) آسیاب های گلوله ای
2) آسیاب های لوله ای
این آسیاب ها همچنین براساس مسیر پیمایش ماده نیز تقسیم بندی می شوند که براین اساس به دو نوع سیستم تقسیم می شوند:
1) سیستم باز
2) سیستم بسته
در مسیر باز مواد فقط یک بار عبور می کند اما در مسیر بسته مواد پس از آسیاب شدن و خردشدن از الکهای با مش معین عبور کرده و موادی که بر روی الک باقی می مانند دوباره به سنگ شکن باز می گردد. البته اکثر آسیاب ها معمولاً دارای سیستم بسته هستند.
البته آسیاب ها را براساس خواص دیگر آنها نیز طبقه بندی می کنند مثلاً براساس حالت مواد مورد خردایش قرار گرفته ولی با توجه به تحولات انجام شده در صنعت سیمان دنیا و تغییر روش ها از روش تر به روش خشک،این تقسیم بندی ها و طبقه بندی ها منسوخ گشته است.
2. 4 خشک کردن مواد اولیه
مواد اولیه معمولاً دارای رطوبت هستند این رطوبت در برخی موارد به 10 تا 12 درصد نیز می رسد. برای داشتن شرایط بهینه درآسیاب کردن و فرآیند پیش گرم کردن مواد اولیه در سیکلون ها باید مواد اولیه رطوبت زیادی نداشته باشند از این رو مواد اولیه خشک می گردند.
برای خشک کردن مواد اولیه معمولاً از روشهای مختلفی استفاده می شود. براساس نحوه ی حرکت مواد اولیه و جریان هوا این تقسیم بندی به صورت زیر است:
1) خشک کن دارای جریان متقابل
2) خشک کن دارای جریان موازی
1. 2. 4. خشک کن دارای جریان متقابل
اساس کارکلیه ی خشک کن ها بر مبنای برخورد مستقیم یا غیر مستقیم مواد با یک سیال گرم است که در طی این برخورد انتقال حرارت مابین سیال و مواد اولیه صورت می گیرد. در خشک کن های جریان متقابل، حرکت سیال و مواد اولیه درخلاف جهت همدیگر است. در این خشک کن از محلی که مواد اولیه خارج می گردد،هوای داغ وارد می گردد. مسأله ی مهم در این خشک کن ها تنظیم دمای مواد اولیه است. باید توجه داشت که دمای مواد اولیه از مقدار معینی بالاتر نرود زیرا این امر موجب تجزیه ی گرمایی کلسیم کربنات می شود.
2. 2. 4. خشک کن دارای جریان موازی
اساس کاراین نوع خشک کن شبیه خشک کن با جریان متقابل است با این تفاوت که جهت حرکت هوا نسبت به جهت حرکت مواد اولیه یکسان است. در این نوع خشک کن از محلی که مواد اولیه خارج می گردد،هوا نیز خارج می گردد.
3. 2. 4.مقایسه ی خشک کن دارای جریان موازی با نوع دارای جریان متقابل
توانایی خشک کن با جریان متقابل کمتر از توانایی خشک کن های با جریان موازی است. همچنین احتمال کلوخه شدن مواد اولیه درانتهای خشک کن جریان متقابل به دلیل افزایش ناگهانی دمای مواد اولیه در انتهای خروجی مواد، وجود دارد. در کل در صنایع سیمان بیشتر از خشک کن با جریان متقابل استفاده می کنند.
3. 4. پیش گرم کردن مواد
پیش از ورود مواد مهیا شده (آسیاب شده) به داخل کوره ی پخت کلینکر،این مواد باید پیشگرم شوند. مزیت پیش گرم شدن مواد این است که بازده کوره پخت کلینکر افزایش می یابد و در ضمن طول کوره نیز کاهش می یابد. این مسائل موجب کاهش هزینه ی نگهداری و هزینه ی اولیه ی احداث کارخانه می گردد و برای ما مفید می باشد عمل پیش گرم شدن مواد در سیکلون ها اتفاق می افتد. سیکلون ها ساختاری است استوانه ای که انتهای پایینی آن تنگ می گردد. و اساس کار این وسیله بدین صورت است که با حرکت مواد و هوای داغ (سیال داغ) از داخل این وسیله،دمای مواد افزایش می یابد. برای افزایش بازده سیکلون،طراحی به گونه ای است که مواد اولیه در داخل سیکلون به صورت مارپیچ (مترگونه) حرکت می کنند. (مواد اولیه از بالا به پایین می آیند). سیال نیز که عمدتاً یک هوای گرم شده است از بخش پایینی سیکلون وارد می گردد. شکل خاص سیکلون و وجود پره هایی در داخل سیکلون باعث می شود که جریان هوای وارده به شکل گردابی (چرخشی) در آمده. که این حرکت گردابی به مواد اولیه یک نیروی گریز از مرکز وارد می کند و باعث تجمع ذرات درشت در یک محل خاصی می شود. با تجمع ذرات در کنار هم این ذرات به هم چسبیده (سنگین می شوند) و از سیکلون خارج می گردند.
جریان هوایی که از پایین وارد پیش گرم کن می شود ذرات را به دو قسمت تقسیم می کند. یکی از تقسیم بندی ها ذراتی هستند که نیروی اصطکاک آنها با هوا بیشتر از نیروی وزن آنهاست. که این غلبه ی نیروی اصطکاک بر نیروی وزن باعث حرکت آنها به سمت بالای سیکلون می شود. و تقسیم بندی دوم ذرات درشت است که به پایین حرکت می کنند پس در هر سیکلون از بالا به پایین ذرات درشت تر می شوند.
معمولاً در کارخانجات سیمان بخش پیش گرم کن از 4 یا 5 سیکلون تشکیل شده است. که دمای ورودی به این سیکلونها در حدود 1100 درجه سانتیگراد و هوای خروجی در حدود 330 درجه سانتیگراد است. ورود هوا بسیار گرم این مطلب را متذکر می شود که سیکلون ها در تماس با هوای 1100 درجه سانتیگراد را باید با آجر نسوز عایق کاری کنیم.
با حرکت خوراک اولیه در طی این سیکلون ها، دمای خوراک به حدود 800 درجه سانتیگراد می رسد. ضمناً خوراک با طی سیکلون ها در زمان 25 ثانیه به انتها می رسند.
ذرات بسیار ریز از بالای سیکلون ها خارج گشته (بوسیله ی جریان هوا) وارد فیلترها می شود. این فیلترها از دو نوع فیلترهای کیسه ای (بگ فیلتر) یا الکتروفیلتر هستند. در فیلترهای کیسه ای جریان هوا وارد یک کیسه می شود که در درون این کیسه ذرات مواد باقی مانده و جریان هوا تصفیه می گردد. در الکتروفیلتر نیز اعمال یک میدان الکتریکی باعث جذب بار ذرات گشته و ذرات نهایتاً تجمع یافته و براساس افزایش وزن آنها،ذرات به پایین الکتروفیلتر می ریزند. در کارخانجاتی که می خواهند عمل فیلتراسیون هوا به شکلی کامل تر انجام شود،از دو نوع این فیلترها به صورت سری استفاده می کنند.
4. 4. کوره ی پخت کلینکر
در کارخانجات تولید سیمان بیشترین هزینه مربوط به کوره است. حداکثر ظرفیت کوره بستگی به قطر کوره، میزان چرخش کوره و شیب کوره دارد.
بنابراینکه تولید کارخانه چه مقداری است و نیاز به کلینکر در کارخانه چه مقدار است،سرعت چرخش کوره تغییر می کند. هر چه سرعت کوره بیشتر شود مقدار کلینکر خروجی بیشتر می شود. این کوره دارای یک شیب ملایم است که هر چه این شیب کمتر باشد میزان انباشتگی مواد بیشتر می شود. هرچه قطر کوره نیز بیشتر باشد،میزان انباشتگی مواد بیشتر می شود ولی باید به این نکته توجه کرد که تشکیل فازهای مناسب در داخل کوره نیازمند انتقال گرمای معینی از سطح توده ی مواد داخل کوره به عمق آن است بنابراین توجه به تنظیم مشعل کوره و میزان انباشتگی مواد اولیه امری حیاتی است و بر روی خواص کلینکر تولیدی اثر می گذارد.
1. 4. 4. نحوه ی چینش آجرها
در کوره ی پخت کلینکر نحوه ی چینش آجرها بدین نحو است که در ابتدای کوره و درجایی که مواد از پیش گرم کن وارد کوره می شوند از بتن های آلومینایی که بیش از 90 درصد آلومینا دارند استفاده می شود. علت استفاده از این بتن ها این است که این بخش از کوره دارای سایش بسیار بالایی است. در واقع خوراک کوره اگرچه ریز هستند ولی به خاطر اینکه ترکیب شیمیایی و مینرالی آنها از مواد اکسیدی با سختی بالاست،سایش شان بسیار زیاد است. این بخش های کوره عمدتاً پس از مدتی ترمیم می گردند.
طول کوره ها 75 متر است که نحوه ی چینش آجرهای آن از ابتدا (محل ورود مواد) تا انتها (محل خروج کلینکر) به صورت زیر است:
1) در سه متر اولیه آجرهای شاموتی که 70 درصد آلومینا دارند .
2) در 25 متر بعدی آجرهای منیزیتی که 80 درصد آنها منیزیا است.
3) در 21 متر بعدی آجرهای شاموتی با 70 درصد آلومینا .
4) در 26 متر آخر آجرهای آلومینایی استفاده می شود.
2. 4. 4. سوخت کوره ی پخت کلینکر
جهت پخت کلینکر سیمان در کوره از سوختهای زغال سنگ، گازوئیل، مازوت و گازطبیعی استفاده می شود. از سوختهای ضایعاتی (Waste Fuels) مختلف نیز می توان به جای سوختهای استاندارد استفاده کرد که این سوختها به عنوان سوختهای جایگزین شناخته می شوند. از جمله سوختهای جایگزین می توان به لاستیک های مستعمل اتومبیل ها، لجن اسیدی (Acid Sludge) که در طول فرآیند عمل آوری نفت خام حاصل می شود. گل رس سفیدکاری. (Bleachinhg clay) که ازجمله ضایعاتی است که درحین استخراج روغن و گریس تولید می شود،روغنهای دورریز و نیز زباله و ضایعات مواد مورد استفاده انسانها اشاره کرد. مقدار کالری تولیدی توسط زغال سنگ با افزایش رطوبت و خاکستر آن کاهش یافته و درمورد گازطبیعی نیز ازمقدار کالری تولید شده با افزایش بخش نیتروژن یا co2 کاسته می شود. معمولاً برای هر 150 کیلوگرم مواد خام اولیه، 20 کیلوگرم سوخت لازم است. البته توجه به خلوص سوخت مصرفی نیز مسأله ای حیاتی است.
انتخاب سوخت برای فرآیند پخت کلینکر یک مسأله ی مهم است.این مسأله با توجه به اقلیم و موقعیت کشور انتخاب می شود. در کشور ما نیز با توجه به وجود منابع عظیم گازطبیعی بهترین گزینه گازطبیعی است. مزایای گازطبیعی علاوه بر هزینه ی کم برای کارخانجات داخلی،آلودگی کمتر نیز هست. ضمناً با استفاده از گازطبیعی احتمال ورود ناخالصی به خوراک کوره از سوخت های جایگزین وجود ندارد. این مسأله بر روی خوردگی دیرگدازهای کوره و کنترل فرآیند پخت کلینکر تأثیر بسزایی دارد. و از دیدگاه بنده خوردگی دیرگدازها را کاهش داده و کنترل وضعیت فرایند پخت کلینکر را نیز آسان تر می کند.
3. 4. 4. کوتینگ در کوره
عوامل مختلف درتشکیل لایه در کوره ی پخت کلینکر تأثیر می گذارد. مثلاً یکی از این عوامل میزان ویسکوزیته ی فاز شیشه ای است. اگر کوتینگ تا حدود 20 سانتیمتر رشد داشته باشد مفید است و به صورت یک لایه ی محافظ عمل کرده و از خوردگی آجرهای نسوز جلوگیری می کند. اگر ضخامت این کوتینگ از 20 سانتیمتر بیشتر شود به آن حلقه (رینگ) می گویند که این رینگ مخرب بوده و احتمال این وجود دارد که رشد آن بیشتر شود و باعث بسته شدن بخشی از کوره بگردد. این بسته شدن می تواند حتی باعث انفجار کوره گردد.
وظایف کوتینگ در کوره:
1) حفاظت آجر نسوز در مقابل حرارت
2) حفاظت از آستر نسوز درمقابل حمله ی شیمیایی ترکیبات کلینکر
3) بهبود یکنواختی کلینکر (فاز شیشه ای بوجود آمده بر روی سطح کلینکر می نشیند و سطح کلنیکر را غیر یکنواخت می کند. با حرکت کلینکر بر روی کوتینگ،سطح کلینکر کاملاً گرد و یکنواخت می شود.)
4) کاهش تشعشع حرارتی
5) حفاظت از بدنه کوره
کلنیکرتولیدی از انتهای دیگر کوره خارج شده و به سرعت سرد می شود این سریع سردکردن بر خواص گیرش سیمان تولیدی اثر می گذارد. سپس کلینکر آسیاب می شود و به صورت یک پودر نرم درمی آید. پودر حاصله بوسیله ی مواد افزونی معین مخلوط می شود و به سمت مراکز مصرف فرستاده می شود.
* استفاده ازمطالب این مقاله با ذکر راسخون بلامانع می باشد.
منبع :مرجع کامل تکنولوژی سیمان/میر مسعود معطر خرازی -تکنولوژی پخت سیمان / محمدرضا عزیزیان

گرم کردن حمام تنها با یک شمع
حمام شیخ بهایی یکی از شاهکارهای معماری و مهندسی جهان است. ایران زمین از داشتن چنین فرزندانی به خود میبالد.
حمام شیخ بهایی مربوط به دوره صفویه است که با مهندسی شیخ بهایی ساخته شده است، سیستم گرمایی این حمام از شاهکارهای مهندسی با استفاده از قوانین فیزیک و شیمی محسوب میشود.
آب این حمام با سیستم "دم و گاز" یعنی از گاز متان فاضلاب مسجد جامع و چکیدن روغن عصارخانه شیخ بهایی که در مجاورت حمام قرار دارد روشن میشده است
عصارخانه محلی برای تهیه روغن از دانههای روغن بوده است.
این حمام با استفاده از این سیستم پیچیده مهندسی به مدت طولانی تنها با یک شمع روشن میشده است.
این حمام از نظر معماری مانند سایر حمامهای دوره صفویه دارای ویژگیهای آن دوران است.
متاسفانه تا مدتی پیش این حمام تاریخی به ذبالهدانی و محل تجمع افراد معتاد تبدیل شده بود و جالب اینکه این حمام 30 وارث پیدا کرده بود!!
چندی پیش حفاظت از این اثر منحصر به فرد آغاز شد و به زودی مرمت آن آغاز خواهد شد.
حمام شیخ بهایی در شعاع یکصدمتری جنوب گنبد نظام الملک (جنوب مسجد جامع عتیق) در محله «در دست» قرار دارد.
تاریخ ساخت آن را سال 1065 عنوان میکنند و طراحی آن را به شیخ بهایی نسبت میدهند.
در اقوال آمده که این حمام اسرار آمیز خزینهای دارد که آب آن خودکار و بدون مصرف انرژی مستقیم گرم میشده است.
البته بنا برنظر رایجانرژی گرمایی حمام از گاز و انرژی مالی فضولات و فاضلاب تامین میشده که از طریق سفالینههای تهیه شده و مکش گازهایی چون متان و اکسید گوگرد استفاده می کرده است.
حمام شیخ بهایی بنایی عمومی بوده که به مرور در تصرف اشخاص درآمده و گفته میشود زمانی حتی کارگر حمام نیز ادعایی از حمام داشته است.
در حال حاضر تا پیش از تملک نزدیک به 30 نفر ادعای سرقفلی و مالکیت این اثر را داشتند.

آجر (1)
منبع : راسخون
مقدمه
آجرها گروهی از مصالح هستند که به صورت صنعتی تولید و جایگزین سنگ شده اند و درحقیقت سنگی ساخته دست بشر هستند، سنگی دگرگون که از تغییر وضعیت خشت پدید میآید. این گروه از مصالح که اولین تولید صنعتی و انبوه مصالح ساختمانی به دست بشر به شمار میآیند براساس نوع مواداولیه، روند تولید و محل مصرف به انواع متنوعی تقسیم می شوند. آجرهای رسی که اولین و فراوان ترین آنها هستند قدمت چندهزار ساله دارند. با پیشرفت تکنولوژی و علم شیمی انواع بی شماری از آجرها با کیفیت های مختلف، ابعاد و شکل ظاهری متنوع راهی بازار مصرف شده اند.
تاریخچه
آجر از قدیمی ترین مصالح ساختمانی است که قدمت آن بنا به عقیده برخی از باستان شناسان به ده هزار سال پیش می رسد.در ایران بقایای کوره های سفال پزی و آجر پزی در شوش و سیلک کاشان که تاریخ آنها به هزاره چهارم پیش از میلاد می رسد پیدا شده است. همچنین نشانه هایی از تولید و مصرف آجر در هندوستان به دست آمده که حاکی از سابقه شش هزار ساله آجر در آن کشور است وازه آجر بابلی و نام خشت هایی بوده که بر روی آنها منشورها قوانین و نظایر آنها را می نوشتند گمان می رود نخستین بار از پخته شدن خاک دیواره ها و کف اجاق ها به پختن آجر پی برده اند .
به اعتقاد باستان شناسان، اولین بار آجر در سرزمین بین النهرین تهیه شده است. به هر صورت باید آجر پس پیدایش آتش و در نواحی که معادن سنگ وجود نداشته اند اختراع شده باشد. نمونه های زیبا و باعظمت کاربرد آجر در معماری ایران باستان نماینده پیشرفت درخشان ایرانیان در تولید و مهندسی کاربرد این مصالح است. در این میان می توان از زیگورات چغازنبیل، ایوان مدائن، کاخ های فیروزآباد و لرستان در قبل از اسلا م و همین طور مساجد جامع اصفهان و یزد، گنبد کاووس و ارگ تبریز مربوط به دوران بعد از اسلا م نام برد.
رمز توانایی آجر در خلق شگفت انگیزترین ساختمان های تاریخ در تناسبات آن نهفته است. این ابعاد در طی زمان متحول شده و در حال حاضر با ساختار و توانایی بدن انسان هماهنگ شده است. ابعاد آجر به طریقی است که به راحتی در یکدیگر قفل و بست می گردند. این خاصیت، کیفیت های مهندسی بی شماری از جمله در محل اتصال دو دیوار به یکدیگر به وجود میآورد. آجرها به کمک ملا ت به یکدیگر متصل می شوند و سطح یکنواختی را به وجود میآورند. این ابعاد متناسب باعث شده است که این مصالح به منظور اجرای دهانه های وسیع به صورت قوس و طاق و گنبد که از زمان قبل از ساسانیان در ایران رواج داشته است، کارآیی منحصر به فردی داشته باشد.
خواص آجر باعث شده است که به عنوان مصالح پرکننده دیوار و سقف از جمله پرمصرف ترین مصالح باشد. زیبایی آجر و الگوی حاصل از آجر چینی باعث شده است که به صورت نما در داخل و خارج بنا مورد استفاده قرار گیرد و هویت خاصی به ساختمان ببخشد. استفاده از آجر به عنوان فرش کف و پلکان، فارغ از مقاومت مطلوب آن ویژگی های اقلیمی این مصالح کویری را بیشتر به نمایش می گذارد.
کوره های آجر پزی ابتدایی بی گمان از مکان هایی تشکیل می شده که در آن لایه های هیزم و خشت متناوبا روی هم چیده می شده است.
فن استفاده از آجر ازآسیای غربی به سوی غرب مصر و سپس به روم و به سمت شرق هندوستان و چین رفته است در سده چهارم اروپایی ها شروع به استفاده از آجر کردند ولی پس از مدتی از رونق افتاده و رواج مجدد از سده 12 میلادی بوده که ابتدا از ایتالیا شروع شد.
در ایران باستان ساختمان های بزرگ و زیبایی بنا شده اند که پاره ای از آنها هنوز پا بر جا هستند. نظیر طاق کسری در غرب ایران قدیم ، آرامگاه شاه اسماعیل سامانی در گنبد کاووس و مسجد اصفهان را که با آجر ساخته اند همچنینی پلها و سد های قدیمی مانند پل دختر سد کبار در قم از جمله بناهای قدیمی می باشند.
انواع آجر در ایران قدیم
در ایران هر جا سنگ کم بوده و خاک خوب هم در دسترس بوده است آجر پزی و مصرف آجر معمول شده است اندازه آجر ایلامی حدود 10×38×38 سانیتی متر بوده پختن و مصرف آجر در زمان ساسانیان گسترش یافته و در ساختمان های بزرگ مانند آتشکده ها به کار رفته است اندازه آجر این دوره جدود 44×44×7تا 8 بوده است و بعد های آن 20×20×3 تا4 سانتی متر کاهش یافت .
در فرش کردن کف ساختمان از آجر بزرگتری به نام ختائی به ابعاد 5×25×25 سانتی متر و یا بزرگتر از آن به نام نظامی در ابعاد 40×4×5 سانتی متر استفاده می شده است از انواع دیگر آجر در گذشته آجر قزاقی می باشد که پیش از جنگ جهانی اول روسها آن را تولید می کردند که ابعاد آن 5×10×20 بوده است آشنایی با آجر و مواد اولیه آن آجر نوعی سنگ مصنوعی است که از پختن خشت خام و دگرگونی آن بر اثر گرما به دست می آید خاک آجر مخلوطی است از خاک رس ماسه فلدسپات سنگ آهک سولفات ها سولفورها فسفات ها کانی های آهن منگنز منیزیم سدیم پتاسیم مواد آلی و...
طبقه بندی آجرها
آجرها را می توان بر اساس ویژگی های مختلف آنها طبقه بندی کرد مثلا می توان آنها را بر اساس ترکیب شیمیایی طبقه بندی کرد یا بر اساس کاربرد،روش ساخت وحتی گروهی از آنها را می توان بر اساس رنگ شان طبقه بندی کرد.
روش نوین امروزی، وسایل فنی زیاد و امکانات فراوانی را به دست معماران داده است که با وجود مدرن بودن، وسیله ای برای شکفتن روح حساس و زیباشناس آنها است. البته تنها آجر وسیله شناخت این زیبایی روحی نیست و عناصر بسیاری نیز این عمل را به خوبی انجام می دهند ولی فرق بین آنها در این است که آجر قابلیت ایفای هر منظوری را دارد و باوجود گذشت قرون متمادی هنوز مدرن است. یک ساختمان آجری جزئی از طبیعت است و همآوایی آن را نه تنها به هم نمی زند بلکه رنگ و فرم بدیعی نیز به آن می بخشد و با این وجود هیچ گاه کهنه نبوده و نیست و همراه با زمان پیش می رود. به هر حال یک ساختمان آجری همانند یک فرش دستباف، ترکیب بدیعی از سلیقه های بی انتهای معماران هنرمند است.
آجر رسی
آجر رسی از قدیمی ترین مصالح ساختمانی که به وسیله بشر تولید شده است، می باشد. سنگ باوجود فراوانی و استقامت به راحتی در دسترس قرار نمیگیرد، این مصالح طبیعی فرم دلخواه را به آسانی به خود نمیگیرد و با صرف هزینه بسیار قطعات آن یکسان می گردند و در این حالت نیز دورریز زیادی از خود به جا می گذارد. در حالی که گل حاصل از خاک رس که منشا تهیه آجر است به راحتی شکل دلخواه را به خود می گیرد و محصولی همگن به دست میدهد.
از این رو می توان با قالب زدن گل و حرارت دادن آن مصالحی سخت، دارای مشخصات فیزیکی، مکانیکی و شیمیایی یکسان، متناسب با کاربرد، منطبق با فیزیک بدن انسان، با فرآیند تولید ساده، سریع و حمل ونقل آسان تولید کرد.
انواع آجر غیر رسی و اشکال آن
آجر جوش آجر خاص در صنعت سفال پزی است که در کشورهای صنعتی دارای اهمیت ویزه ای است از این آجر برای نماسازی ساختمان ها فرش کف پیاده روها پوشش بدنه و کف آبروها و مجراهای فاضلاب و تونل ها و ساختن دودکش ها فرش کف کارخانه ها انبارهای کشاورزی و سالن های دامداری پرورش طیور استخر های صنعتی و جز اینها استفاده می شود.
انواع خاص آجر تولیدی در کشور های اروپایی
آجر هایی در کشورهای صنعتی اروپاتولید می شوند که هنوز تولید آن در ایران مرسوم نشده است از آن جمله بلوک های تو خالی آتش بند برای نصب دور ستون ها به منظور جلوگیری از نفوذ آتش قطعات ویزه به شکل منحنی های کوز و کاس قطعات درپوش روی دیوار قطعاتی که از اجزا هستند مانند کلوک سرقد گوشه و جزاینها که هنوز در ایران تولید نمی شوند.
آجرهای نسوز
از آجرهای نسوز بدلیل مقاومت حرارتی بالا ، در پوشش درونی کورههای صنعتی استفاده میشود. آجرهای نسوز انواع مختلفی دارد. باتوجه به نوع ماده استفاده شده در ترکیبات آنها ، گسترههای مختلفی را تحمل میکنند. تا دهه 1960 از کربن و خاک نسوز برای پوشش کورهها استفاده میشد، اما امروزه با ساخت انواع آجرهای نسوز از آنها در پوشش داخلی کوره استفاده میشود.
درزیر برخی از انواع مختلف آجر دیر گداز توضیح داده شده است
آجرهای سیلیسی
قسمت عمده این آجرها را خاکهای سیلیسی که به کوارتزیت معروف است تشکیل میدهد. کوارتزیت شامل 95% SiO2 و به مقدار جزئی Al2O3 ، Fe2O3 ، TiO2 ، K2O و Na2O میباشد. از این آجرها در گذشته برای پوشش جدار درونی کورههای فولادسازی استفاده میشد.
ولی بدلیل رسانایی گرمایی زیاد در نفوذناپذیری در مقابل گازها ، امروزه بیشتر برای پوشش جدار درونی کورههای تولید خمیر شیشه در کارخانههای شیشه سازی ، کورههای کک سازی گازسوز و کورههای سرامیک سازی استفاده میشود.
آجرهای آلومینیومی
این آجرها ، دارای درصد بالایی از آلومین ( Al2O3) میباشند. آنها را از مخلوط کائولن ، بوکسیت و کروندوم که بیش ار 70% آلومین دارد، تهیه میکنند دمای پخت این آجرها در حدود 1200 تا 1800 درجه سانتیگراد میباشد. آجرهای نسوز آلومینیومی برای پوشش جداره درونی کورههای ذوب فولاد مصرف میشوند.
در مقابل مواد قلیایی مقاومند، بنابراین از آنها برای پوشش جداره درونی کورههای سیمان سازی و شیشهسازی هم استفاده میشود.
آجرهای نسوز قلیایی
این آجرها شامل اکسید منیزیم (MgO) و SiO2 به فرمول 2MgO SiO2 میباشند. برای تهیه اکسید منیزیم ، کربنات منیزیم طبیعی (ماگنزیت یا دولومیت را در دمای بین 550 درجه سانتیگراد تا 1800درجه سانتیگراد حرارت میدهند. اضافه کردن مقداری Cr2O3 ( اکسید کروم III ) یا Fe2O3 ( اکسید آهن III ) به مخلوط MgO و SiO2 باعث افزایش مقاومت گرمایی آجرهای نسوز قلیایی میشود.
از این آجرها برای پوشش جدار درونی کورههای باز در فولادسازی ، کورههای دوار در کارخانههای سیمان سازی و در قسمتهای بالای کورههای ذوب شیشه و صنایع فلزات غیرآهنی ، استفاده میشود.
آجرهای نسوز ویژه
این آجرها نوع خاصی از آجرهای نسوز هستند و در صنعت برای منظورهای ویژهای کاربرد دارند. این آجرها از ترکیبات فلزات واسطه میشوند. متداولترین آجرهای این گروه عبارتند از:
آجر زیرکونیوم
این آجر از سولفات زیرکونیوم طبیعی با افزودن مقدار کمی آلومین به کوارتز تهیه میشود. بیشترین کاربرد آن در ساختن کوره ذوب آلومینیوم ، کوره مخزن شیشه مذاب و کورههای دارای دمای بالا میباشد. همچنین از ذوب سولفات زیرکونیوم با آهک ناخالصی آن به همراه سیلیکات کلسیم جدا میشود و میتوان ) ZrO2 اکسید زیرکونیوم) خالص بدست آورد. با افزودن مقدار 5 درصد وزنی از MgO یا CaO ، بلورهای مکعبی آن تشکیل میشود.
ZrO2 مقاومت گرمایی بالایی دارد، بهمین دلیل از آن در ساختن بوتههای ذوب فلز در صنایع ذوب فولاد و در راکتورهای اتمی به عنوان بازتاب دهتده نوترون استفاده میشود.
آجر اکسید کروم – کوروندوم
این آجرها دارای 5 تا 10 درصد اکسید کروم I , II و 90 تا 95 اکسید آلومینیوم (Al2O3) هستند و در مقابل مواد قلیایی مقاوم هستند. از این نوع آجر برای ساختن بخش درونی کوره بلند ذوب آهن استفاده میشود.
آجرهای اکسید کروم
دارای 95 درصد Cr2O3 میباشد. برای تهیه آن از Cr2O3 سنتزی استفاده میشود. این نوع آجر در ساختن کوره ذوب خمیر شیشه مخزن در صنعت شیشهسازی مصرف دارند.
در جدول 1 دمای ذوب انواع آجرهای دیرگداز آورده شده است.
آجرها از لحاظ روش ساخت به دو نوع تبدیل می گردند. در واقع این تقسیم بندی بر اساس نحوه ی تولید ایجاد گشته است. بر اساس روش ساخت آجرها به صورت زیر طبقه بندی می شوند:
1- آجرهای فشاری :
دلیل نامگذاری این نوع آجر اینست که در ابتدای تولید این نوع آجر، خشت آن با دست زده میشد و با فشار دستی کارگران خشت زن گوشههای قالب به وسیله گل مخصوص پر میگردید. ابعاد این نوع آجر 5×10×20 و یا 5/5×11×22 سانتیمتر است.
این نوع آجر برای کلیه کارهای ساختمانی مانند گرهچینی، طاق ضربی، دیوارهای حمال و تیغه چینی مناسب است.
2- آجرهای ماشینی :
آجر ماشینی یا آجر سوراخدار که بر روی سطح بزرگتر آن 8 یا 10 سوراخ به قطر 1/5 تا 2 سانتیمتر وجود دارد و در بازار ایران به آجرهای هشت یا ده سوراخه ماشینی معروف است.
در استاندارد شماره 7 موسسه استاندارد و تحقیقات صنعتی ایران این سوراخها باید تمام ضخامت آجر را طی نموده و سطح مقطع مجموع سوراخها نباید بیشتر از 25 درصد سطح بزرگتر آجر باشد و فاصله سوراخها از لبه آجر و همچنین فاصله سوراخها از یکدیگر در هر بعد آجر نباید کمتر از 30 درصد طول همان بعد باشد.
علت وجود این سوراخها اینست که در هنگام دیوارچینی ملات به طور عمودی نیز در آجر نفوذ کرده و باعث استحکام بیشتر دیوار شود.
در ساخت دیوارهای حمال به دلیل اینکه میتوان به وسیله سوراخهای موجود در سطح آجر آنرا با میلگرد، مسلح کرد از این نوع آجر استفاده میشود. دیوار آجری مسلح برای مقابله با نیروی زلزله ساخته میشود.
جنس این نوع آجرها نسبت به آجرهای فشاری بسیار ترد و شکننده بوده و خاصیت مکندگی آن نسبت به آجر فشاری کمتر است. این آجرها به علت ترد بودن قابل تیشهداری نیستند و همچنین بهدلیل اینکه خاصیت مکندگی زیادی ندارند و نمیتوانند به خوبی به ملات بچسبند در طاق ضربی استفاده نمیشوند.
ابعاد این نوع آجر 5/5×11×22 سانتیمتر میباشد. اضلاع این نوع آجر گونیاتر بوده و دارای سطوح صافتری نسبت به آجرهای فشاری میباشند.
طبقه بندی از لحاظ رنگ
در صورت استفاده از آجر در نماچینی رنگ آجر اهمیت پیدا میکند. برای استفاده در نماچینی آجرهایی به رنگهای زرد کمرنگ که به آن آجر سفید میگویند و زرد پررنگ که به آن آجر بهی میگویند و همچنین آجرهایی به رنگ قرمز روشن یا قرمز سیر در بازار وجود دارند.
در حدود سالهای 1320 تا 1340 یک نوع آجر ابلق به رنگهای قرمز و زرد بنام آجر بهمنی به بازار عرضه میشد که بوسیله کوره آجرپزی به همین نام تهیه میگردید.
ضخامت آجرهای مورد استفاده در نما ممکن است 3 تا 4 یا 5 سانتیمتر باشد ولی دو بعد دیگر این آجرها مانند آجرهای فشاری یا ماشینی 10×20 میباشد.
علت رنگی بودن این آجرها مربوط به طریقه چیدن آجر در کوره و نحوه آتش دادن به آن و کنترل سطوحی که با آتش در تماس مستقیم میباشد است و یا مربوط به اکسید فلزاتی است که در مواد اولیه آجر موجود میباشد. مانند اکسیدهای مختلف آهن.
برای تهیه مصالح اولیه و همچنین مراحل خشتزنی و خشتخشککنی آجرهای رنگی دقت و هزینه بیشتری به عمل میآید.
بر طبق استاندارد شماره 7 ایران آجرهای مصرفی در نما باید دارای مشخصات زیر باشند:
1) معایب ظاهری :
آجرنما باید عاری از معایب ظاهری مانند ترک خوردگی، شوره زدگی، آلوئک و نظایر آن باشد.
2) لبه های آجر :
خط فصل مشترک سطوح آجرها باید مستقیم و زوایای تلا قی آنها قائمه و سطوح شان صاف باشد.
3) در آجرهای سوراخ دار :
سوراخ ها باید عمود بر سطح بزرگ آجر و به طور یکنواخت در سطح آن توزیع شده باشند و جمع مساحت آنها باید بین 25 تا 40 درصد سطح آجرها باشد. بعد سوراخ های مربع و قطر سوراخ های دایره ای باید حداکثر به 26 میلیمتر محدود شود و در ضخامت دیواره بین سوراخ و لبه آجر بیش از 15 میلیمتر و فاصله بین دو سوراخ بیش از 10 میلیمتر باشد.
4) مقاومت در برابر یخبندان :
آجرهای مصرفی در نما باید در برابر یخبندان پایدار باشند و در آزمایش یخ زدگی دچار خرابی ظاهر مانند ورقه ورقه شدن، ترک خوردن و خوردگی نشوند.
قطعات نازک آجری (آجر دوغایی) مورد مصرف در نماسازی به ابعاد 20* (40 یا 30) * 200 میلیمتر با قطعات موزائیکی نازک آجری نما به ضخامت 20 یا 30 میلیمتر با نقش چند آجر بندکشی شده (آجر موزاییکی) ساخته می شوند حداقل باید دارای مشخصات آجرهای ماشینی با مقاومت متوسط مندرج در استاندارد شماره 7 ایران باشند.
5) ترک در سطح آجر :
وجود یک ترک عمیق در سطح متوسط آجر حداکثر تا عمق 40 میلیمتر در آجر پشت کار بلا اشکال است ولی به طور کلی درصد آجرهای ترک دار نباید بیشتر از 25 باشد.
6) پیچیدگی ، انحنا و فرورفتگی :
پیچیدگی در امتداد سطح بزرگ آجر حداکثر 4 میلیمتر و در امتداد سطح متوسط آجر تا 5 میلیمتر مجاز است. آجر نباید انحنا و فرورفتگی بیش از 5 میلیمتر داشته باشد و این مقدار در صورتی قابل قبول است که میزان آن از 20 درصد کل آجرها افزایش پیدا نکند.
7) سایر موارد :
آجر باید کاملا ً پخته و یکنواخت و سخت باشد و در برخورد با آجر دیگر صدای زنگ دار ایجاد کند. به علت عدم چسبندگی آجرهای کهنه به ملا ت حتی المقدور از آنها استفاده نمی شود و تنها در صورت انجام پیش بینی های لازم به صورت ساییدن یا برس سیمی استفاده از آن مجاز خواهد بود.
آجرهای ساختمانی مقاومت خوبی در برابر آتش دارند به طوری که یک دیوار 22 سانتی متری از آجر در حدود شش ساعت در برابر آتش سوزی مقاومت از خود نشان می دهد.
انواع آجرها از نظر نوع مصرف
آجر معمولی :
آجرهائی هستند که برای کارهای عمومی ساختمان مناسب هستند و به روش دستی یا ماشینی تولید می شوند.
آجرنما :
بطریق خاصی ساخته می شود تا هنگام مصرف بدون نیاز به اندودکاری یا روکش های دیگر خود، دارای ظاهر مناسبی باشد، این نوع آجر هم می تواند به روش دستی (قزاقی) یا ماشینی تولید شود.
آجر مهندسی مرغوب :
این آجر دارای جسمی متراکم، پرقدرت و نیمه شیشه ای است و عمدتاً در سازه های با قدرت تحمل بار زیاد بکار برده می شود. این آجر منحصراً به روش ماشینی تولید می شود.
انواع آجرها از نظر کیفیت
آجر با کیفیت مناسب برای مصارف داخلی (توکار) :
این آجر برای مصارف معمولی در داخل ساختمان بکار می رود.
آجر با کیفیت معمولی:
این نوع آجرها دارای دوامی کمتر از آجرهای با کیفیت ویژه ولیکن معمولاً در نماهای خارجی ساختمان دوام کافی را خواهد داشت.
آجر با کیفیت ویژه :
این نوع آجر در شرایط سخت و ویژه کاربرد دارد نظیر مناطقی که از آب اشباع شده یا یخ زدگی ممکن است رخ دهد نظیر : دیوارهای حائل، کانال های فاضلاب، فرش پیاده روها و غیره
درجه حرارت لازم برای پخت آجر بستگی به نوع خاک و تعداد عناصر معدنی موجود در خاک دارد. درجه حرارت مناسب بین 900 تا 1200 درجه می باشد.
انواع آجرها از نظر شکل
آجر توپر :
که در آن حجم سوراخ ها از 25 درصد حجم آجر (یا در حالت آجرهای پرسی، حجم فرورفتگی از 20 درصد آجر) تجاوز نمی کند. در این نوع آجر سوراخ ها کاملاً یا تقریباً از میان آجر عبور می کنند
آجر سوراخ دار :
که در آن حجم سوراخ هائیکه از میان آجر می گذرد از 25% حجم آجر بیشتر باشد.
آجر توخالی :
که در آن حجم سوراخ هائیکه از میان آجر عبور می کنند از 25% حجم آن بیشتر است و هیچگونه محدودیتی در ابعاد سوراخ ها وجود ندارد.
آجر متخلخل :
که در آن حجم منافذ (سوراخ های بسته شده در یک انتها) بیش از 20% حجم آجر باشد. نکته مورد توجه این است که آجرهای متخلخل معمولاً با روش های پرسی تولید می شوند و آجرهای سوراخ دار و توخالی با استفاده از روش دکسترودر (برون رونده) ساخته می شوند.
آجر با شکل مخصوص :
که دارای شکل هندسی بغیر از مکعب مستطیل معمولی هستند.

آجر (2)
منبع : راسخون
مراحل ساخت آجر
1) کندن و استخراج مواد خام
2) آماده سازی مواد اولیه
3) قالب گیری
4) خشک کردن
5) پخت آجر
کندن و استخراج مواد خام
ماده اولیه آجر را عمدتا خاک رس تشکیل می دهد همانگونه که می دانید , انواع مختلفی ازخاک رس وجود دارد , ولی بیشتر ازخاک رس آبرفتی برای تهیه استفاده می شود .
در مناطق مختلفی از ایران منابع مطلوب از مواد اولیه وجود دارد که کارگاه های تولید آجر چه به صورت سنتی یا مدرن در کنار این معادن احداث می گردد. البته برخی از کارگاه های تولیدی معدن مواد اولیه ندارند و مواد اولیه ی مورد نیاز خودرا از سایر معادن خریداری می کنند و در محل کارگاه دپو می کنند.
در زیر مواد مورد نیاز برای تولید آجر آورده شده است:
خاک رس آبرفتی :
همانطوری که از نامش پیداست در نزدیکی سطح زمین یافت می شود و بیشتر آجر های رسی باکمک آن تولید می شوند . میزان خاک رس در گل آجر بسیار اهمیت دارد . خاک رس زیاد گل آجر را توپر می کند ولی موجب ترک خوردن خشت در هنگام خشک شدن می شود .
ماسه :
که از تاثیر عمل فرسایش هوازدگی بر سنگ های سیلیسی حاصل می شود درحقیقت استخوان بندی آجر می باشد . در صورت افزایش مقدارآن آجر ترد وپوک می شود وضمنا دانه های درشت ماسه درگل آجر درهنگام پختن منبسط وموجب ایجاد ترک های ریز درآجر میشوند .
آهک :
درخاک رس و گل آهک وجود دارد , درصورتیکه به صورت دانه ریز , یکنواخت وهمگن باشد وموجب روشن شدن رنگ آجر می شود وافزایش مقدارآن نقش گدازآوردارد.وجوددانه ها ی درشت آهک درگل آجر پس از پختن آهک زنده تولید میکند . آهک زنده درهنگام استفاده از آجر ,آب ملات رابه خود می کشد وتولید هیدرواکسید آهک یا آهک شکفته می کند ,که بسته به خلوص سنگ آهک 25/1 تا 5/3 برابر حجم اولیه را به دست می آوردو موجب ترکیدن آجر می شود به این پدیده آلوئک آجر می گویند .
ترکیبات سولفاتی :
به مقدار کم بی ضرر است و درصورت افزایش , تولیدیون اسیدی می نمایند و به آجر و ملات آسیب می رسانند .
ترکیبات آهن دار :
نقش گداز آور دارند و رنگ محصول را به قرمز نزدیک می کنند .
نباتات و ریشه گیاهان :
ممکن است در گل آجر ریشه گیاهان وجود داشته باشند که در حرارت کوره می سوزاند وآجر پوک میشودو پس از تهیه ماده اولیه آن را الک و خوب آسیاب می کنند تا نرم ویکنواخت شود .(معمولا باانتخاب منبع خوب برای خاک رس این مشکل راتاحدی حل می کنند )
آماده سازی مواد اولیه
عملیات های مورد نیاز جهت آماده سازی مواد اولیه به نحوه ی پروسه ی تولید بستگی دارد.
برای تهیه خشت آجر رسی سه روش متفاوت وجود دارد که درهر روش میزان رطوبت خاک و نوع گل متفاوت است .
1) گل خشک
که با اضافه نمودن آب به میزان حدود 8 تا 12 درصدوزن ماده اولیه تهیه میشود و باکمک پرس خشت شکل می گیرد . بسیاری از آجرهای صنعتی ووکلیه سفال های ساختمانی با روش گل خشک ساخته می شوند .
2) گل سفت
که با اضافه نمودن آب به میزان حدود 20 تا25 درصد وزن ماده اولیه تهیه می شود و با روش ماشینی خشک می زنند . در این روش از ماشین های خشت زنی هیدرولیکی استفاده میکنند خشت U به صورت منشوری با قاعده مربع یا مستطیل شکل از دستگاه خارج می شود وسپس آن را به کمک دستگاه برش به قطعات مساوی تقسیم می کنند .
3) گل خمیری
بااضافه نمودن آن به میزان تاحد 60 درصد وزن به خاک تهیه می شودتا حالت خمیری پیداکنند وبتوان با دست به آن شکل داد . دراین روش گل را درون قالبهای چوبی می ریزند و بادست شکل می دهند و خشت می زنند .
خشک کردن
زمانی که قطعات ازماشین های شکل دهی خارج می شوند مقدار قابل توجهی رطوبت به همراه دارند . خشک کردن خشت خام قبل از پختن آن به علت جلوگیری از تغییر شکل زیاد وترک در سطح خشت می باشد وهمچنین از صرف هزینه سوخت بیشتر درکوره اصلی و امکان دوده گرفتن کوره به سبب رطوبت اولیه زیاد وسوخت ناقص جلوگیری می کند . درکارخانه به روش سنتی 1ـ 2 هفته ودرکارخانه به روش صنعتی 36 ساعت .
خشک کردن موجب بروز انقباض می شود و این انقباض درحدی مجاز است که محصول نهایی دارای اندازه مناسب و دلخواه باشد .
جمع شدگی در خشت خشک شده حدودا ده درصد در هر بعد است . درجه حرارت کوره خشک کن درهر بعد است .درجه حرارت کوره خشک کن از 40 تا 200 درجه سانتیگراد و زمان خشک کردن از 24 تا 48 ساعت متغیر است که بستگی به نوع رس دارد . حرارت لازم معمولا به کمک گرمای تلف شده از کوره های اصلی فراهم میشود . درکلیه مراحل , حرارت ورطوبت کاملا تنظیم می گردند تا از انقباض سریع که موجب به وجود آوردن ترک های زیاد میشود , اجتناب گردد .
درمناطق گرم و خشک ازگرمای هوا به منظور خشک نمودن خشت استفاده می کنند دراین روش نحوه چیدن خشت ها ازاهمیت فراوان برخور دار است . به ترتیبی که جریان هوا یک جانبه نباشدچون باعث ایجادانحنا و تغییر شکل آجر در اثر خشک شدن یک جانبه می شود .
خشت خشکی که برای پختن آجر آماده شده است رطوبتی بین 8 تا 12 درصد به همراه دارد .
پخت آجر
گداختن یکی ازمهمترین قدم ها درساختن آجر می باشد .زمان موردنیاز باتوجه به نوع کوره , نوع رس و سایر متغیرها از 40 تا 150 ساعت تغییر می کند درحال حاضر کوره های تونلی و کوره های متناوب انواع جدیدی ازکوره ها میباشند که مورد استفاده قرارمی گیرند . درکوره تونلی آجرهای خشک شده که برروی واگون ها ی مخصوص چیده شده انداز داخل تونل گذر می کنند و از کانون حرارتی عبورمی نمایند واز سوی دیگرخارج می شوند .( آجر بعد از پخته شدن یک مر تبه از کوره خارج نمی شود چون ترک میخورد و طی زمان 6 ساعت به صورت یکنواخت ازکوره خارج میشود )
درکوره های دیگر , حرارت به طور متناوب تغییر می کند دراین روش خشت ها ثابت وکانون حرارتی متغیر است . سوخت این کوره هاگاز طبیعی ,نفت یاز غال سنگ می باشد .
کنترل زمان پخت درکوره ازاهمیت فراوانی برخوردار است خشت خام فاقد مقاومتهای مکانیکی مورد نظر است وچنانچه آجر بیش از حد حرارت ببیند تغییر چنانچه آجر بیش از حد حرارت ببیندن تغییر شکل می دهدو قابل استفاده نمی باشد .
به منظور اجتناب ازبروز ترک حرارت تا دمای 100 تا 120 درجه سانتیگراد به کندی افزایش می یابد دراین دما آب آزاد خشتها تبخیر وخشک می شود . بعد ازخشک شدن خشت ها حرارت به سرعت 5 تا 700 الی 800 درجه سانتی گراد افزایش می یابد و در این دما آب تبلور کائولن تبخیر ( دی هیدراته ) می شود وخشت ها نهایت تخلخل خود را پیدا می کنند دردمای 800 تا 850 درجه سانتیگراد مواد زود گداز همراه با رس گداخته میشوند واجزای دیرگداز را احاطه می نمایندوبعد طولی رس ها نقصان می یابد و خشت حرارت دیده به مصالح یکپارچه ای تبدیل میشود .
مصالح تشکیل شده از رس زودگذر دردرجه حرارت بین 900 و 1100 درجه سانتیگراد کاملاگداخته می شوند و مصالح ساختار سنگی پیدا می کند این مصالح به خوبی در برابر نفود آب مقاوم است ومقاومت مکانیکی بالا, مقاومت دربرابر یخبندان و سایر کیفیات یک مصالح ارزشمند را پیدا می کند .
دربعضی ازروشهای نوین به منظور جلا یافتن سطح آجردرمرحله نهایی با تزریق گاز طبیعی سطح آجر می سوزد و تغییر رنگ می دهد و جلا پیدا می کند .
برای جلوگیری ازترک, آجر ها را به عنوان آهستگی سردمی نمایند و بعد از آن کنترل نهایی انجام می گیرد و در صورت نیاز به منظور یکنواختی ماشین کاری وسپس آجر های مرغوب بسته بندی ,انبار یا بارگیری میشوند .
انواع کوره های آجر پزی
پس از خشک شدن خشت , انرا درکوره میچینند بطوریکه که به همدیگر نچسبند , تا هوا شعله وگا ز از لای آجرها بگذرند . کوره های آجرپزی سه نوع اند :
1- کوره با آتش ثابت و آجر ثابت
2- کوره با آتش رونده و آجر ثابت
3- کوره با آجر روند وآتش ثابت
1) کوره با آتش ثابت و آجر ثابت یا کوره تنوره ایی
این کوره کارش پیوسته نیست کوره تنوره کوتاه وگشادیست که خشت را درآن می پیچنند و تون آنرا می تابند ( آتش می کنند ) شعله , هوای داغل و دود ازلا به لای خشت های چیده شده درکوره بالا می روند و گرمای خود را به خشت ها پس می دهند وخشت ها می پزند .
کار کوره تنوره ایی پیوسته نیست و در آن گرمای زیاد ی هدر میرود زیرا پس از آنکه خشت پخته شد و آجرشد , سر کوره را باز می کنند ومی گذارند تا آجر درون کوره سردشود وگرمایش را به هوابدهد .
جنس آجر ی که درکوره تنوره یی پخته شود یک جور نیست . از پایین به بالاجوش , آجرجوش ,آجر سبز , آجر بهی , آجر سفید , آجر ابلق , آجر قرمز و آجر نیم پخته بدست می آید . اگربالای کوره های تنوره یی به شکل قارچ ساخته شده و سر کوره پوسیده شود , جوری که گاز کوره از بالای آن بیرون نرفته از سوراخ های نزدیک کف کوره به دو دکش یاهواکش مکیده شود گاز داغ ,گرمایش رابه خشت های چیده شده در کوره پس می دهدو با این کار ,گرمای گاز کوره هدر نمی رود و جنس آجرها هم همجور می شود .
2) کوره با آتش رونده و آجر ثابت
کار این کوره پیوسته است و گرمای آن خیلی کم هدر می رود این کوره را نخست یک بنای اهل برلن به نام Friedrich Hoffmann ساخت که به نام او نامیده می شود . چون حلقه ایی ساخته میشد آنرا کوره حلقه ایی هوفمان نامیدند .
نخستین کوره ها به شکل دایره ساخته میشدند ,اکنون آنرا به شکل حلقه دراز یا اره ایی و مانند اینها می سازند در این کوره ازهدر رفتن گرما به اندازه زیاد جلوگیری می شود .
3) کوره تونلی
در آن سفالهای ممتاز هم می پزند . کارش مانند تونل خشت خشک کنی ست از سر تونل واگونک با بار خشت به تونل می رودو از ته تونل آجرسرد شده بیرون می آید کانون آتش در دیوار درونی تونل جا دارد همین که واگونک با بار خشت به درون تونل رانده شد ,به کندی به سوی کانون آتش پیش می رود خشت کم کم گرم و نیم پز شده از برابر کانون آتش گذشته می پزد .
هنگامیکه واکونگ آجر پخته به سوی ته تونل می رود ,به آن هوای سرد می دمند تا گرمای آجر را بگیرد و آنرا سرد کند هوایی که از روی آجر گذشت و داغ می شود و هواکش پهلوی کانون آتش آنرامکیده و به کانون آتش می دمد . کارکوره تونلی پیوسته است و گرمای آن خیلی کم هدرمی رود اما ساختن تونل ریل گذاری , ارزش واگونک ها وجزاینها گرانست . جایی که برق ارزان باشد ,می شود کوره تونلی را برقی ساخت وکوره را با برق آتش کرد .
برای آنکه کوره تونلی دراز نشود , آنرا در دوتکه پهلوی هم می سازند دریک تکه خشت میسازند وروی واگونک می چینند وبه گرمخانه می برند تا درآنجا خشتهای روی واکونگ ها خشک ,گرم و داغ شوند , سپس واکونگ های بابار خشت داغ را به درون تکه دوم میرانند درتکه دوم که کوره درآن ساخته شده , خشت های داغ شده از برابر کانون آتش گذشته میپزند روی آجر داغ هوا می دمند و گرمای آنرامی گیرند . هوای داغ شده را به گرمخانه و به کانون آتش می دمند .
نتیجه گیری
در صنعت آجر حدود 7000 کارخانه فعال در ایران موجود است که میزان تولید اسمی سالیانه آنها بیش از 50 میلیون تن میباشد. محصولات اکثر این کارخانجات، شامل آجر سنتی، آجر ماشینی و بلوک تماما با فنآوری قدیمی تولید میشوند که علاوه بر انرژیبری بسیار بالا در تولید (بیش از 2 برابر انرژیبری تولید آجر با فنآوری جدید)، از بسیاری از مزایای نهفته در استفاده از آجرهای جدید بیبهره میباشند. سهم 45 درصدی هزینههای انرژی در تولید آجر از دیدگاه اقتصاد ملی، خود بیانگر شدت انرژی مصرفی بسیار بالا در این صنعت و لزوم توجه به آن میباشد.
راهکارهای بهینهسازی مصرف انرژی
1) راهکارهای کوتاه مدت و کم هزینه.
2) راهکارهای بلندمدت و پرهزینه.
اجرای راهکارهای کوتاهمدت و کمهزینه در مقایسه با راهکارهای بلندمدت و پرهزینه از نظر اجرا، عملیتر و برای صاحبان واحدهای تولیدی نیز قابل قبولتر میباشد. با توجه به اینکه در کشور نزدیک به 7000 کوره آجرپزی وجود دارد, بهترین راهکارهای کمهزینه استفاده از مشعلهای با راندمان بالا در کورههای هوفمن موجود و بازیافت حرارت از این کورهها است.
راهکارهای کم هزینه و کوتاه مدت
1) استفاده از سوختپاشهای راندمان بالا در کورههای هوفمن با حدود 20 درصد صرفهجویی.
2) بازیافت حرارت در کورهها.
3) آموزش پرسنل.
4) استفاده از مشعلهای با راندمان بالا.
5) بازیافت حرارت از کورههای هوفمن جهت استفاده در قسمت خشک کن.
راهکارهای پرهزینه و بلند مدت
1) جایگزینی ماشینآلات مدرن در خط تولید شامل تجهیزات، سنگشکن، میکسر، اکسترودر.
2) نصب خشککن با راندمان بالاتر و کاهش ضایعات و مصرف انرژی کمتر.
3) جایگزینی کوره تونلی بجای کوره هوفمن که دو تا سه برابر شدت مصرف انرژی را کاهش میدهد.
4) استفاده از سیستم بستهبندی مدرن بمنظور کاهش ضایعات.
تنوع تولید آجر در کشور
همانگونه که در نمودار 1 مشاهده می شود، بیشترین سهم تولید آجر کشور مربوط به آجرهای فشاری می باشد که این خود گویایی پایین بودن کیفیت آجرهای تولیدی و همچنین بالا بودن میزان مصرف سوخت در این صنعت می باشد.
در نمودار 2 سهم استان های مختلف کشور از مصرف مجموع حامل های سوخت در گروه صنعتی آجر، کاشی، سرامیک و چینی نشان داده می شود.
مقایسه مصرف انرژی حرارتی در تولید آجر ماشینی در ایران و برخی کشورهای اروپایی در نمودار 3 دیده می شود.
لازم به ذکر است که دستورالعمل معیار مصرف سوخت برای واحدهای تولیدی آجر که دارای خشک کن هستند، 80 لیتر معادل نفت کوره بر تن آجر تولیدی (معادل 3.45 مگاژول بر تن) و برای واحدهای تولید کننده آجر که خشک کن ندارند، 55 لیتر معادل نفت کوره بر تن تولیدی می باشد.
باتوجه به ساختار کارخانجات سنتی در کشور عزیزمان ایران این مسئله ضروری به نظر می رسد که باید توجه خاصی به مسئله ی بهینه سازی سوخت در صنعت آجر گردد واین مهم انجام نمی شود مگر با برنامه ریزی منسجم و منظم که در آن باید به دو مقوله ی راهکارهای کوتاه مدت و دراز مدت توجه خاص گردد. در این میان هر کدام از افراد شاغل در این زمینه باید آموزش داده شود . در واقع مسئله ی بهینه سازی مصرف انرژی جز با فرهنگ سازی در میان خیل وسیع تولید کنندگان آجر امکان پذیر نمی باشد.
بسیاری از تولیدکنندگان آجر تلاش دارند تا مصرف انرژی را در کارگاه یا کارخانه ی خود پایین آورند اما نحوه ی آن را نمی دانند. پس در مرحله ی اول باید افراد شاغل در زمینه ی تولید آجر آموزش و آگاه سازی شوند.
در مرحله ی دوم باید امتیازات تشویقی همچون وام های با بهره ی مناسب و وام های بلا عوض برای نوسازی و بهینه سازی سایت های تولید آجر به تولید کنندگان داده شود تا عاملی در جهت بهینه سازی درازمدت در انرژی باشد.

کریت اولین سد قوسی جهان
قدیمی ترین و منحصر به فردترین سد قوسی دنیا حاصل محاسبات دقیق معماران ایرانی دوران باستان است
هنر معماران قدیمی کشورمان به خصوص در دوران ایران باستان هنوز هم مایه شگفتی معماران امروزی است که حتی با دقیق ترین محاسبات ریاضی و فیزیک هم نتوانسته اند به رمز و راز این ساخت و سازهای شگفت انگیز که در گوشه و کنار کشورمان به چشم می خورند پی ببرند. « سد کریت» یکی از این سازه های منحصر به فرد است که می توان آن را حاصل نبوغ معماران ایرانی در قرن های گذشته دانست؛ سدی قدیمی در طبس که عنوان اولین سد قوسی جهان را یدک می کشد.
شاید خیلی ها نمی دانند که از 2 هزار سال پیش تا اوایل قرن بیستم، بلندترین سدهای قوسی جهان مثل ایزدخواست فارس، کبار قم و کریت طبس، در ایران ساخته شده بودند. آن موقع هنوز گینس پا به دنیا نگذاشته بود و خبری از ثبت رکوردهای اینچنینی نبود، در غیر این صورت حتماً اسم سد باستانی و زیبای کریت، به عنوان رکورددار بلندترین سد در جهان ثبت شده بود. محاسبات به کار رفته در ساخت این سد آنقدر دقیق است که رئیس سابق کمیته بین المللی سدهای بزرگ، سد کریت را شگفت آورترین ساخته دست بشر در قرون وسطی می نامد.
سد دو قوسی و بسیار قدیمی کریت، در فاصله 50 کیلومتری جنوب شرق شهرستان طبس در یزد و در میان رشته کوه های برافراشته شتری قرار گرفته است. بعد از طی 50 کیلومتر در جاده طبس- دیهوک، مسیری وجود دارد که به روستای سروند می رسد و بعد از گذشتن از این روستا، جاده وارد روستای دیگری به نام ماودر می شود. تا اینجا مسیر، ماشین روست، ولی اگر می خواهید این سد منحصر به فرد را از نزدیک ببینید از اینجا به بعد باید کفش آهنین به پا کنید! چرا که حدود ده کیلومتری را باید پیاده طی کنید.
این مسیر صعب العبور پر است از صخره های آهکی ستبر و زیبا؛ در طول مسیر می توانید از دیدن آبشارها هم لذت ببرید تا طولانی بودن راه را حس نکنید!
البته وقتی به این نکته فکر کنید که حدود هزار سال پیش، سازندگان این شاهکار مصالح مورد نیازشان را برای ساخت این سد با مشقت و سختی زیاد از همین راه و از میان تخته سنگ ها، کوه ها و آبشارها عبور می دادند حتماً ذوق و شوقتان برای رسیدن به انتهای مسیر و تماشای سازه دست ساز آنها بیشتر می شود. البته بهتر است بدانید که این مسیر صعب العبور تقریباً به همان شکل گذشته اش باقی مانده و تغییر زیادی نکرده.
اسم سد کریت، از اسم روستایی گرفته شده که در 40-30 کیلومتری این سد قرار دارد. مهم ترین نکته ای که درباره این سد وجود دارد، نحوه مکان یابی ساخت این شاهکار توسط معماران و سازندگان آن در آن دوران است؛ اینکه آنها در آن سال ها، چطور به این نکته پی برده اند که این مکان، مناسب ترین محل برای ساخت چنین سدی است؟!
سد ضد زلزله
دکتر یعقوب دانش دوست- دکترای معماری و شهرسازی- است و تجربیات فراوانی در مرمت بناهای تاریخی دارد، او یکی از افرادی است که تحقیقاتش درباره این سد را در قالب یک کتاب منتشر کرده است؛ او می گوید:« روش سدسازی به شکل قوسی، روشی قدیمی در ایران است.
سد کریت با وجود گذشت سال ها هنوز هم شکل قوسی خودش را حفظ کرده و در عکس های هوایی گرفته شده هم، این موضوع به خوبی قابل مشاهده است. البته سدهایی با فرم قوسی شکل، مقاومت بسیار بالایی دارند و در مقابل فشارهای ناگهانی مثل زلزله، ریزش کوه و حوادث طبیعی مقاومت خوبی از خودشان نشان می دهند.»
زمین لرزه، واکنش طبیعی زمین در مقابل انرژی زیادی است که در طی سال ها در آن انباشته شده؛ یعنی زمین با ایجاد لرزش، در ریشترهای مختلف، انرژی اش را تخلیه می کند. مردم کشورهایی که روی نوار زلزله خیز کره زمین زندگی می کنند، خاطره خوشی از این لرزش ها ندارند. اینها را گفتیم تا از مقاومت سد کریت در برابر یک زلزله قدرتمند بگوییم که سال ها پیش اتفاق افتاده و این سد از آن جان سالم به در برده است. دکتر ناظمی، محقق و زمین شناس در این باره می گوید:« 25 شهریور ماه 1357، زمین لرزه ای با قدرت 7/4ریشتر طبس را لرزاند. این سد با وجود اینکه در معرض یک زلزله شدید قرار گرفت اما نه تنها تخریب نشد که حتی ترک هم برنداشت.»
اما قبل از اینکه درباره نوع ساخت و مصالح به کار رفته در بدنه این سد ضد زلزله صحبت کنیم، بهتر است اطلاعاتی درباره شکل ظاهری سد کریت داشته باشید. دکتر ناظمی در این باره می گوید: « ارتفاع قسمت بیرونی سد از کف رودخانه، 52 متر و عمق حوضچه آبگیر 20 متر و طول آن در قسمت تاج 52 متر و ضخامت تاج هم 1/2 متر است. نکته جالب اینجاست که سد کریت محل مخصوصی برای خروج آب اضافی بعد از پر شدنش ندارد، برای همین آب های اضافی ناشی از سیلاب ها، بعد از پر شدن سد، از روی بدنه سد بیرون می ریخته و این موضوع نشان می دهد که بدنه سد بسیار محکم ساخته شده که با وجود گذر سیلاب های زیاد از روی آن خراب نشده است.»
مصالحی که در ساخت بدنه سد به کار رفته، جالب است. ناظمی درباره این مصالح می گوید:« مصالحی که در ساخت سد به کار رفته ساروج و سفیده تخم مرغ بوده. تخم مرغ همیشه ماده بسیار ارزشمندی بوده اما چون می خواستند سد مقاوم باشد، از چسبندگی تخم مرغ در بدنه سد استفاده کرده اند. ماده اصلی به کار رفته در بدنه سد هم ملات آهک و شن و خاک است که مقاومت زیادی در برابر انحلال و تخریب دارد.» سازندگان علاوه بر استفاده از ساروج و ملات، در زمان های دیگر هم که سد به تعمیر احتیاج داشته، از آجر و سنگ استفاده کرده اند.
معماران این سد 700 سال پیش، برای ساخت آن، یک دره تنگ و باریک و برای جمع شدن آب هم یک دشت نسبتاً صاف را در نظر گرفته بودند. این سد در دو مرحله کامل شده است. حدود 150 سال قبل چهار متر به ارتفاع سد اضافه کردند که هم برای افزایش بهره وری از سد بوده و هم این که مانع از متروکه شدنش می شد.
سدهای به صرفه
سدها انواع مختلفی از نظر شکل و نوع معماری دارند؛ «آنها سه نوع هستند. تک قوسی، دو قوسی و سه قوسی. یک سری از سدها هم سدهای معمولی هستند که به دو دسته خاکی و بتونی تقسیم می شوند. در سدهای معمولی باید بدنه سد را مقاوم و با ضخامت زیاد بسازیم تا با وزن خودش جلوی فشار آب را بگیرد. این سدها مصالح ساختمانی زیادی مصرف می کنند اما در سدهایی که به شکل قوس هستند، چون محل قوس به درون سد است، انرژی و نیروی زیاد فشار آب را خود سد تحمل نمی کند و آن را به دیواره های کوه منتقل می کند. سدهای قوسی باید در دره باریکی ساخته شوند و دیواره هایشان هم باید آن قدر مقاوم باشند که فشار زیاد آب را تحمل کنند.» اینها را دکتر ناظمی می گوید و ادامه می دهد؛ « سدهای قوسی به خاطر اینکه از مصالح کمی در ساخت آنها استفاده می شود، خیلی به صرفه تر هستند. به خصوص اینکه سد کریت در یک منطقه صعب العبور واقع شده و حمل و نقل مصالح در این مسیر خیلی سخت بوده و بنابراین بهترین راه این بوده که سازندگان بتوانند با مصالح کم این بنا را برپا کنند. سد امیرکبیر هم یکی از سدهایی است که به شکل قوسی ساخته شده. البته سدهای قوسی معایبی هم دارند. مثلاً شرایط زمینی و محیطی خاص برای ساخت آنها باید وجود داشته باشد. مانند سد کریت که در دره تنگ قرار دارد.»
فکر بکر
سدهای قوسی مثل سد کریت مزایا و معایب مختلفی دارند اما نکته دیگری که درباره سد کریت وجود دارد این است که آب این سد در زمان های کم آبی و خشکسالی هم نسبتاً خوب است. سازندگان این سد خلاقیت و ابتکار منحصر به فردی را در ساخت آن از خود نشان داده اند مثلاً در دریاچه سد یک چاه حفر کرده اند که به برج آبگیری معروف است. دکتر ناظمی در این باره می گوید:« یک برج آبگیری به شکل یک چاه متصل به سد، در وسط دریاچه ساخته شده که به خاطر افزایش فشار آب در قسمت های عمیق دریاچه، از بالا به پایین ضخامت و قطرش زیاد می شود. در داخل چاه موجود در برج آبگیری، سوراخ هایی وجود دارد که به درون دریاچه منتهی می شود. محلی ها به این سوراخ ها قفل می گویند. قطر این سوراخ یا قفل ها بین 20-10 سانتی متر است. این قفل ها به شکل دایره هستند و داخل آن چوب یا پارچه می گذاشتند و با پتک به آن می زدند تا محکم شود و آب بند بیاید. البته این سوراخ ها در فواصل و ارتفاع های مختلف و بسیار منظمی از هم ساخته شده اند.»
در دوران گذشته، مردمی که از آب سد کریت استفاده می کردند در مواقع خشکسالی به سراغ آب ذخیره شده در چاه می رفتند؛ « در زمان های کم آبی قنات ها و آب های زیر زمینی و با توجه به کاهش آب سد یا دریاچه در زمان های مختلف، یک کارگر ماهر که خیلی هم شجاع بوده، وارد این چاه می شده و چوب یا پارچه ای را که سوراخ گرفته بوده بر می داشته. به این ترتیب تراز پایین تری از آب سد تخلیه می شده و به این شکل آب از زیر سد عبور می کرده و به مصرف مردم روستای کریت می رسیده. در فصول آبگیری که نزولات جوی مثل باران زیاد بوده، همه سوراخ های باز شده را دوباره می بستند و سد دوباره پر از آب می شد.»
در حال حاضر دیگر از سد کریت برای ذخیره آب استفاده نمی شود، چون عمر مفید سد تمام شده و به گفته دکتر ناظمی، به جز 5-6 متر از داخل سد که قابل استفاده است، داخل آن پر از رسوب شده و عدم لایروبی در طول زمان، مانع از آبگیری مجدد آن می شود.
البته در حال حاضر از این سد به صورت ویژه نگهداری نمی شود چون چند وقتی است که بالاتر از این سد، یک سد بتونی و وزنی به شکل قوسی ساخته شده؛ « همین که سد جدیدی برای آب گیری ساخته اند و آب به سد تاریخی کریت فشار نمی آورد، باعث می شود احتمال تخریب آن از بین برود.» نوع ساخت سد کریت به قدری خاص و مبتکرانه است که بسیار مورد توجه کارشناسان خارجی قرار گرفته است. این سد باستانی در سال 1379، در فهرست آثار ملی کشور به ثبت رسید.
700 یا 1000 ساله
اختلاف نظرهای فراوانی در مورد قدمت سد باستانی کریت طبس وجود دارد
درباره قدمت سد کریت اختلاف نظر وجود دارد. به گفته دکتر محمد ناظمی- زمین شناس- شواهد و اسناد تاریخی بر جای مانده نشان می دهند یکسری تعمیرات در اواسط قرن پنج روی این سد زیبا انجام شده که این به معنای آن است که این سد قبل از قرن پنج و بیش از 700 سال است که ساخته شده اما از طرفی زرتشتیان هم مدارکی دارند که نشان می دهد آنها سازنده سد کریت هستند که اگر فرض را بر این ادعا بگذاریم، زمان ساخت سد به قبل از اسلام خواهد رسید. از طرفی پروفسور هانری گویلو که 30 سال روی قنات های ایران تحقیق کرده ساخت این سد را به دوران مغول نسبت داده است. دکتر ناظمی درباره قدمت سد کریت می گوید:« به این حکایت دقت کنید: در تاریخ کرمان، اشاره ای به تعمیر بند( سد) کریت شده است:« ملک قارود پس از رفتن برادر( آلب ارسلان) سفری به بلوچستان و جیرفت نمود و بر این بلاد امیر و نواب معین نمود و بند ( سد) طبس را تعمیر کرد و با توجه به این نوشته سد کریت در اواسط قرن پنج تعمیر شده است و این نکته را نشان می دهد که زمان ساخت این سد قبل از قرن پنجم بوده.» معنی حرف دکتر ناظمی این است که عمر سد بیش از هزار سال است. هر چند محلی ها همچنان اصرار دارند که این سد باستانی متعلق به 700 سال پیش است. دکتر یعقوب دانش دوست هم درباره قدمت سد می گوید:« سد کریت بسیار قدیمی است و عده ای می گویند که در دوران پیش از اسلام و توسط زرتشتی ها ساخته شده. من در این خصوص تحقیقاتی داشته ام که در کتابم منتشر شده اما مطالعه بقایای به جای مانده از نوع ساخت و نحوه معماری نشان می دهد که این سد متعلق به 700 سال پیش است.»
منبع:هفته نامه همشهری سرنخ، شماره
کاربرد پوشانه های ETFE در ساخت پوسته های اقلیمی و هوشمند
مهندس الهام سرکرده ئی (2)
ETFE covers for making intelligent continental layers
چکیده
امروزه فویل های ETFE، در کنار مصالحی نظیر شیشه، پلی کربنات و اکریلیک و ... ازجمله مصالح مورد استفاده در پوشش های ساختمانی هستند که معمولاً هم در نما و هم در نورگیرهای سقفی استفاده می گردند. کیفیت ویژه ی این مصالح ساختمانی نظیر شفافیت زیاد، مقاومت عالی در برابر آلودگی های محیطی و خاصیت ضد چسبندگی، مقاومت بالا در برابر تابش فرابنفش و عمر مفید طولانی، سبکی و بی خطر بودن، امکان تنظیم شفافیت و جلوه ی بصری پوسته و ... آن را به یکی از کم رقیب ترین مصالح جهت ساخت پوسته های اقلیمی و هوشمند تبدیل کرده است. این مقاله ضمن معرفی این ماده، مهم ترین خواص و ویژگی آن را با ذکر مصادیق مختلف مورد بررسی قرار می دهد.
تصویر 1: باغ وحش برگر(Berger) در آرنهایم (Arnheim) هلند (1982): یکی از اولین نمونه های کاربردETFE درجهان
کلید واژه ها: فویل ETFE، شفافیت، سبکی، دوام، قابلیت تنظیم.
مقدمه
بیش از بیست و پنج سال است که فویل ها برای مسقف کردن سازه ها مورد استفاده قرار گرفته اند. این فن آوری مبتکرانه در آغاز برای پوشش استخرهای شنا و ساختمان های باغ وحش استفاده شد (تصویر 1). امروزه این سیستم ابتکاری که در آن شفافیت و وزنِ سبک با ویژگی های عایق کاری بسیار عالی و طول عمر زیاد ترکیب شده و در توسعه ی معماری، پیشگام است توسط معماران مشهوری نظیر نیکولاس گریمشاو، مایکل هاپکینز، نورمن فاستر، آلسوپ و ... استفاده می شود. درحال حاضر، فویل ها به عنوان راه حل استاندارد مسقف کردن فضاهای محصور اداری، نورگیرهای سقفی کارخانه ها و ... و به طور کلی ساخت پوسته های ساختمانی متناسب با اهداف عملکردی و زیبایی شناسانه بنا، در حال استفاده اند.
جدول 1: ویژگی های سازه ای فویل های ETFE
ضخامت (میکرون) |
ون ) |
مقاومت کششی |
کرنش کششی (درصد) |
مقاومت گسیختگی (N) |
50 |
5/87 |
56/64 |
450/450 |
450/450 |
80 |
140 |
54/58 |
600/500 |
550/450 |
100 |
175 |
57/58 |
600/550 |
440/430 |
150 |
5/262 |
57/58 |
650/600 |
420/450 |
200 |
350 |
52/52 |
600/600 |
430/430 |
250 |
5/437 |
40 > /40 > |
300 > /300 > |
300 > /300 > |
معرفی ماده و خواص آن
فویل ETFE، کوپلیمری از اتیلن و تترافلوئور اتیلن، یک پلاستیک بی نهایت پایدار است که در برابر هر نوع بارگذاری و عامل محیطی نظیر اشعه ی ماورای بنفش، آلودگی هوا، فضولات پرندگان و ... مقاومت می کند و ترکیبات فیزیکی و شیمیایی آن در طول زمان تغییر نمی کند.
نقطه ی ذوب آن حدود 250 تا 270 درجه ی سانتی گراد، چگالی اش بین 73/1 تا 77/1 گرم بر سانتی متر مکعب و در ضخامت های مختلف از 50 تا 250 میکرومتر ساخته می شود.
فویل های ETFE بسیار شفاف اند و گذردهی نور آن ها بین 90 تا 95 درصد است. این شفافیت در بیش تر طیف الکترومغنایس اتفاق می افتد و شامل طیف فرابفنش (UV) هم می شود که برای رشد گیاهان و فتوسنتز ضروری است.
این ماده خویشاوندی نزدیکی با تفلون دارد و خاصیت نچسب بودن آن ها به کی میزان است. رسوباتی مانند کثیفی، گرد و خاک و ذرات خرد به سطح این ماده نمی چسبند و توسط باران شسته می شوند، لذا در زمره ی مواد خود شست و شو (self cleaning) محسوب می شوند.
به دلیل مقاومت عالی آن در برابر تابش فرابنفش (UV)، طول عمر متوسط آن به بیش از سی سال می رسد.
غشاهای ETFE، مصالحی تقریباً ایزوتروپیک هستند که دارای خواص نسبتاً یکسان در جهات مختلف اند در جدول 1 خلاصه ای از ویزگی های سازه ای این ماده در دو جهت طولی (L or Longitudinal) و عرضی (T or Transversal) آورده شده است.
سیستم پوشانه ی ETFE:
طرح کلی سیستم پوشانه ی ETFE شامل دو لایه یا بیش تر از فیلم های ETFE می شود که لبه های آن ها جوش حرارتی داده می شود تا به شکل یک قطعه ی بالشتکی که قابل باد شدن است درآیند. (تصاویر 2 و 3)
برای ساخت یک بالشتک حداقل دو فویل مورد نیاز است. لایه های بیش تر ویژگی های عایق کاری را بهبود می بخشند، گرچه در مقابل، شفافیت غشا را تقلیل می دهند. سپس این فویل ها به یک نیم رخ آلومینیومی اکستروژن شده پیرامونی محکم می شوند که خود نیز قاعدتاً به یک نوع سازه زیرین پیچ شده است این سازه می تواند چوب چند لایه، فولاد، آلومینیوم، یا سیستم های کابلی باشد. (تصاویر 4 و 5)
ویژگی های بالشتک های ETFE :
به طور قطع ویژگی های بالشتک ETFE مربوط به خواص فویل های سازنده ی آن است که به طور اجمالی ذکر شد. اما چون این ماده معمولاً در پوسته های ساختمانی به صورت بالشتک های باد شده ی چند لایه به کار می رود، در ادامه مهم ترین ویژگی های این سیستم پوشانه بیش تر تشریح می شود.
امکان تنظیم شفافیت پوسته
ساختمان چند لایه ی بالشتک ها به طراح فرصت های بی شماری می دهد تا مقدار سایه اندازی پوسته ی بنا را کنترل و شفافیت بصری آن را مدیریت نماید. این ویژگی، توسعه ی محیط هایی با مصرف کم انرژی و مهندسی طبیعی را ممکن ساخته است.
استفاده از روکش های انتخاب کننده (selective coating) بر روی فویل های کارآیی آن را در شرایط گوناگون افزایش می دهد. روش های کنترل انکسار نور در طول موج های 300 تا 800 نانومتر نیز در وضوح بصری پوشانه نقش مهمی دارد و امروزه دستیابی به وضوح (clarity) کامل تقریباً میسر است (تصویر 6)
بر روی بالشتک های ETFE می توان الگوهای گرافیکی از پلیمرهای فلوئور نیمه شفاف یا مات را چاپ کرد. با استفاده از این بالشتک ها، طیف وسیعی از سایه اندازی قابل وصول است در عین حال که شفافیت بصری پوسته نیز حفظ می شود، فویل ETFE می تواند با یک ته رنگ نیمه شفاف تولید شود. با تغییر دادن تعداد و نوع لایه ها، چگالی و رنگ آن ها، خواص گذردهی نور را می توان به طور نامحدود تغییر داد. رنگ های استاندارد موجود عبارت اند از سفید، آبی، زرد، قرمز و سبز. (تصویر 7)
کنترل انرژی خورشیدی و پوسته های متغیر
ساختمان چند لایه بالشتک ها می تواند برای ایجاد پوسته های اقلیمی که محیط خود را حس می کنند و درجه عایق بودن خود و گذردهی نور خورشید را در صورت نیاز تغییر می دهند، به کار گرفته شود.
با چاپ کردن طرح های گرافیکی دارای همپوشانی بر روی لایه های متعدد و یکی کردن بالشتک ها با سیستم های پنوماتیک پیچیده، می توان طرح های گرافیکی مختلف را همراه با هم و جدا از هم حرکت داد. با این روش می توان هم مقدار جذب انرژی خورشیدی نفوذ کرده در بنا و هم سیمای بصری پوسته را تغییر داد. این پدیده را نه تنها می توان برای کنترل مقدار انتقال نور خورشید از میان پوسته به خدمت گرفت، بلکه می توان برای تغییر تعداد محفظه های هوا در درون یک بالشتک نیز مورد استفاده قرار داد و به وسیله ی آن مقدار U برای بالشتک تغییر داده شود.
این خواص منحصر به فرد طراحان را قادر می سازد تا ساختمان هایی خلق کنند که کارآیی انرژی و صرفه جویی اقتصادی دارند و نسبت به تغییرات شرایط محیطی عکس العمل بصری دارند.
به طور کلی به منظور مقاومت در برابر گرمای بیش از حد از طریق تشعشع مستقیم خورشید چندین امکان وجود دارد تا از درجه حرارت نامناسب در فضای داخل اجتناب گردد. در مورد تشعشع مستقیم بسیار شدید خورشید سه راه حل ممکن وجود دارد: (تصاویر 8 تا 13)
1- سایه اندازی بیرونی پوسته؛
2- سایه اندازی درونی پوسته؛ و
3- کنترل پویا و متغیر به کمک پُر و خالی کردن باد محفظه های مختلف.
جدول 2: مقدار U برای بالشتک های چند لایه ETFE
تعداد فویل ها |
مقدار U ، بر حسب |
2 |
94/2 |
3 |
96/1 |
4 |
47/1 |
5 |
18/1 |
عایق کاری، تهویه
بالشتک های ETFE از 2 تا 5 لایه ی فویل ساخته می شوند. چون هر لایه ی فویل یک لایه ی هوا را محصور می کند، مقدار U برای پوسته بسیار پاین است و می تواند متناسب با نوع کاربرد، بهینه سازی شود. (جدول 2) به منظور افزایش کیفیت بالای عایق کاری پوسته می توان از روکش های انتخاب گر نیز استفاده کرد.
علاوه بر پایین بودن استثنایی مقدار U، اتلاف گرما در اثر تراوش (infiltration) نیز در درون سیستم به صفر کاهش می یابد، به طوری که بالشتک ها یک حصار محافظ دارای فشار تنظیم شده را در پیرامون ساختمان شکل می دهند.
علاوه بر کنترل مقدار U و جذب انرژی خورشیدی، می توان بازشوهای تهویه در پوسته ی بنا نیز تعبیه کرد. پوشانه ی ETFE در میان فن آوری های ساختمانی منحصر به فرد است، چرا که انعطاف پذیری بالا آن را قادر می سازد تا تهویه ی های بسیار بزرگ تر و سازه های متحرکی ساخت که با فن آوری های معمول پیشین، امکان آن نبود. (تصویر 14)
دوام، سازگاری با محیط زیست و پایداری
فویل ETFE از آلودگی جوی و اشعه UV متاثر نمی شود. این ماده در طی زمان سخت نمی شود، زرد نمی گردد و تنزل کیفی پیدا نمی کند. این ویژگی ها استفاده از آن را برای بناهای نیازمند عمر طولانی و هزینه نگهداری کم، نظیر بیمارستان ها، ایستگاه های راه آهن، مراکز تفریحی و مراکز گیاه شناسی ایده آل می سازد. همچنین، قابلیت آن در شست و شوی خود در اثر برخورد باران، هزینه های دوره ی بهره برداری را بسیار کاهش می دهد.
فویل ETFE هم کارآیی انرژی دارد و هم از فن آوری دوستدار محیط زیست برخوردار است. این ماده به صورت خام تحت معاهده مونترال پذیرفته می شود و از مشتقات پتروشیمی نیست. تولیدآن یک فرآیند پایه ی آبی بسته است و در تهیه ی آن از هیچ حلالی استفاده نمی گردد.
این مصالح 100 درصد قابل بازیافت است و بسیاری از اعضای سیستم از مواد قابل بازیافت ساخته می شوند؛ به مجرد خرابی محصول، فویل ها به شرکت سازنده بازگردانده می شوند تا بازیافت شوند. فلوریت که از مواد اولیه ی سازنده ی غشاهای ETFE می باشد، یک عنصر رایج است که در سراسر جهان یافت می شود. این محصول بسیار سبک وزن است (وزن سیستم تقریباً 2 کیلوگرم بر مترمربع است) و برای حمل و نقل این سیستم نسبت به ساختمان مشابهی از جنس شیشه یک دهم انرژی مورد نیاز است. مقطع پیچیده اکستروژن ها محیط محافظت شده ای را برای واشرها و درزگیرها فراهم می کند تا از هر گونه خرابی عادی و یا نیاز به نگهداری حفظ شوند.
بنابراین پوشانه ی ETFE یک فن آوری با صرفه ی انرژی بسیار بالاست؛ هم به دلیل عملکرد محیطی اش یعنی عایق قوی بودن و کنترل بهینه ی انرژی خورشیدی، و هم انرژی نهفته ی پایین آن (کم تر از یک درصد فن آوری های رایج).
ویژگی های سازه ای
بالشتک های ETFE را می توان در اندازه های بزرگ ساخت و می توانند دهانه های بسیار بزرگ تری را نسبت به فن آوری های پوشانه ای مرسوم پوشاند. این ویژگی برای طراحان فرصتی را فراهم می کند تا طرح پوشانه را با سازه ی اولیه یکپارچه نمایند و زیبایی سادگی و ظرافت را به نمایش گذارند. (تصویر 15)
سختی ذاتی این مصالح، مقاومت بالا در برابر پارگی و قابلیت سخت شدن ورای دامنه ی ازدیاد طول آن (جدول 1). به این معناست که این سیستم می تواند به طور طبیعی با خیزهای بسیار بزرگ در سازه تکیه گاهی سرو کار داشته باشد. این امر، ساخت سازه های سبک وزن منحصر به فرد نظیر توری های کابلی تک محوره و ژئودزیک های بزرگ مقیاس را ممکن می سازد. (تصویر 14)
با توجه به این که تنظیم فشار بالشتک ها با باد صورت می گیرد، نیروهای ایجاد شده در بالشتک ها توسط تورم (باد شدن) و بارهای خارجی نظیر باد و برف باید توسط سازه اولیه تحمل شوند. بارهایی که تحمیل می شوند تابع دهانه ی بالشتک ها و میزان بالا آمدگی آن ها هستند.
به دلیل ویژگی های فیزیکی فویل ها، محاسبات مهندسی آن ها کاملاً با محاسبات مهندسی استاندارد تفاوت دارد. کشسانی بالای آن در محدوده ی الاستیک و پلاستیک تعیین نقطه گسیختگی فویل و ضرایب ایمنی مورد نیاز که باید دخیل شوند را مشکل می سازد. داده های مصالح ثابت نیست. اما بستگی به نوع بارگذاری و چگونگی اعمال بارها بر محصول دارد.
آتش
این ماده در موسسات گوناگون اروپایی، آزمایشات گسترده ای را پشت سر گذاشته است و دارای خاصیت منحصر به فرد «تهویه ی خودکار» موادحاصل از احتراق به بیرون می باشد. در شرایط آتش سوزی، هر گاز داغی که در دمای بالای حدود 200 درجه سانتی گراد به بالشتک ها برخورد می کند، فویل را گرم می کند. از آن جایی که فویل تحت کرنش ناشی از تورم است، در اثر زبانه های آتش خراب، و به عقب جمع می شود و به طور موثری آتش را به هوای آزاد بیرون می دهد. هر یک از تکه های فویل که هنوز باقی است، توسط زبانه های آتش به سمت بالا رانده می شود و از آنجا که ذرات ماده مورد استفاده در سقف بسیار کوچک ا ند، کسی چکه های ETFE مذاب را که به زمین می افتند حس نمی کند. (تصویر 16)
این ویژگی تهویه ی خودکار، از انباشت گازهای بسیار گرم در زیر ساختمان سقف و در نتیجه از امکان جرقه و انفجار و یا واژگونی فاجعه بار سازه اصلی جلوگیری می کند.
این سیستم را می توان با سیستم مدیریت ساختمان به کار انداخت و به حس گرهای گرما، دود، باد و باران مرتبط کرد. از سبکی و انعطاف پذیری ETFE می توان بهره ی بیش تری گرفت و بازشوهای بسیار بزرگ تری در سقف طراحی کرد تا دهلیزها و فضاهای بازِِ محصور (آتریوم ها) بتوانند در شرایط آتش سوزی تهویه ی بهتری را انجام دهند.
نقطه ی ذوب ETFE تقریباً 275 درجه ی سانتی گراد است، گرچه در زیر این درجه حرارت نیز نرم می شود. وجود فلوئورین در ساختار ETFE، این ماده را خود خاموش شونده کرده است.
آزادی فرم و امکان ایجاد جلوه های بصری
این محصول اساساً با هر شکلی خود را تطبیق می دهد و می تواند برای پوشش شکل هایی که در فضا می پیچیند نیز به کار می رود. (تصویر 17)
بالشتک های ETFE امکانات زیبایی را همراه با سیستم نورپردازی پیش روی طراحان قرار می دهند. (تصویر 18)
در طرح مرکز ملی بازی های آبی در پکن، معماران پروژه از ویژگی شکلی بالشتک های ETFE در ایجاد ساختمانی با سیمای حباب گون بهره گرفته اند. (تصویر 19)
جمع بندی
سیستم پوشانه ی ETFE، فرصت های بی مانندی را در مسیر توسعه ی پوسته ی اقلیمی برای طراحان فراهم می کند. این سیستم تشکیل شده است از بالشتک های بادی که توسط پروفیل های اکستروژن شده آلومینیومی، مهار می شود و به وسیله ی یک سازه ی سبک وزن نگه داشته می شوند. این بالشتک ها به منظور عایق شدن و تأمین مقاومت در برابر باد با فشار کم هوا باد می شوند.
این بالشتک ها از کوپولیمر اتیلن تترافلوئور اتیلن اصلاح شده ETFE و بین دو تا پنج لایه ساخته می شوند. این مصالح منحصر به فرد که در اصل برای صنعت فضانوردی ایجاد گردید، در برابر تابش فرابنفش یا آلودگی جوی تنزل کیفی پیدا نمی کند. این بالشتک ها به دلیل این که بسیار با دوام هستند می توانند به عنوان بخشی از پوسته های ساختمانی دائمی مورد استفاده قرار گیرند. به علاوه، به دلیل سطح بسیار نرم و خاصیت ضد چسبندگی این بالشتک ها، پوسته ی بنا با برخورد باران، خودش تمیز می شود. فویل ETFE، گذردهی استثنایی نور را با عایق کاری بسیار عالی ترکیب می کند. این لایه ها می توانند درجات مختلفی از سایه اندازی را ایجاد کنند و طراح را قادر می سازند تا عملکرد محیطی و زیبایی شناسانه ی پوسته ی ساختمان را بهینه نماید. حتا می توان سیستم های پوشانه ای ایجاد کرد که در برابر تابش خورشید عکس العمل نشان دهند و میزان گذردهی نور و عایق بودن خود را در طول روز تغییر دهند.
از طریق تحلیل بار و الگوسازی پیچیده می توان این بالشتک ها را به هر شکل و اندازه ای در محاسبات مهندسی منظور نمود. انعطاف پذیری ذاتی ETFE، به طراحان این امکان را می دهد تا سازه هایی با سبکی و ظرافت نامتعارف خلق نمایند.
این خواص پوشانه ی ETFE، همراه با میزان بسیار کم انرژی نهفته و ویژگی های محیطی برجسته ی آن، تحقق پوسته های واقعاً اقلیمی – طبیعی را ممکن می سازد.
پینوشتها:
1- کارشناس ارشد معماری، طراح، محقق و مدرس معماری، m.mojahedi@gmail.com
2- عضو هیئت علمی گروه معماری دانشگاه صنعتی شاهرود
منابع
[1] Rogier Houtman: “There is no material like membrane material”, Designing Tensile Architecture, Vrije universiteit, Brussel, 2003, page 180-191.
[2] Brian Forster, Marijke Mollaert” “European Design Guide for Tensile Surface Structures”, Vrije universiteit, Brussel, 2004, page 45,220,221
[3] Stefan Lehnert” “Intelligent Roof Systems: Foil Cushions”, The Design of membrane and lightweight structures, Vrike universiteit , Brussel, 2002, page 125-130.
طراحی بهینه ی ژئوتکنیکی پی های عمیق (4)
ضریب اطمینان در تعیین ظرفیت بار محوری شمع
پس از استنتاج توان باربری شمع به یک یا چند طریق اعم از آنالیز استاتیکی، استفاده از نتایج آزمایش های درجا، آنالیز دینامیکی تست های دینامیکی و آزمایش بارگذاری در مقایس واقعی، با اعمال ضریب اطمینان بر Ru مقدار Ra بار مجاز فشاری و یا کشش به دست می آید. برای شمع تحت بار فشاری مقدار ضریب اطمینان در محدوده ی 2 تا 4 و برای بارهای کشش مقدار ضریب اطمینان در محدوده ی 3 تا 5 در تغییر بوده که به عواملی از قبیل نوع و اهمیت روسازه، عواقب حاصل از خرابی روسازه، نوع خاک، گستردگی مطالعات ژئوتکنیک، تعداد و نوع آزمایش های آزمایشگاهی و درجا، انجام آزمایش های بارگذاری استاتیکی و دینامیکی، تحلیل با استفاده از آنالیز معادله ی موج، چگونگی ساخت و نحوه ی بازرسی ها و کنترل در محل، احتمال اعمال بارهای زنده بر سازه و چگونگی ارزیابی آن ها، طراحی شمع بر مبنای نتایج فرمول های شمع کوبی، نحوه ی تفسیر آزمایش، بارگذاری بستگی دارد.
مقدار ضریب اطمینان به میزان پذیرش عواقب مربوط به انهدام و همچنین آگاهی و کنترل جنبه های مؤثر در تغییرات ظرفیت باربری در سایت بستگی دارد. در روش های سنتی و قدیمی، ضرایب اطمینان در تعیین ظرفیت باربری شمع بر پایه ی تغییر شکل های مجاز شمع به دست می آمد. بار مجاز Ra بالای شمع را می توان کوچک ترین دو مقدار زیر در نظر گرفت:
- تا زمانی که ایمنی در برابر ظرفیت نهایی شمع مدنظر است، نیازی به تحلیل دقیق در تفاوت بین ایمنی برای باربری کف و ایمنی برای مقاومت جداری نمی باشد. این که حداقل ضریب اطمینان از طریق باربری کف و یا مقاومت جداری تأمین می گردد خیلی مهم نیست.
- برعکس، در تحلیل ضریب اطمینان مسائل با ماهیت تغییر شکلی، تفاوت در جابه جایی های مربوط به مقاومت بسیج شده ی انتهایی و جداری یقیناً نقش بسیار مهمی ایفا می نماید.
در مجموع با استفاده از روش های مکمل اعم از آنالیز استاتیکی، تست های درجا، آنالیز و تست های دینامیکی، آزمایش بارگذاری مطالعات ژئوتکنیک مناسب و استفاده از تجارب و قضاوت مهندسی می توان ضریب اطمینان را تا حدود 5/1 کاهش داده و صرفه جویی مناسبی در هزینه و زمان اجرا به عمل آورد (Fellenius, 1990).
فونداسیون های رادیه مرکب (1)
در طراحی فونداسیون ها متداول است که جهت انتقال بارهای روسازه به خاک، رادیه به عنوان کامل ترین گزینه مدنظر قرار می گیرد. این پی ها در مواردی از قبیل بزرگ بودن بارهای روسازه، ضعیف بودن شرایط خاک بستر و نشست های ناهمسان، زمین های مستعد تورم، توزیع غیریکنواخت بارهای جانبی و بالا بودن سطح آب زیرزمینی، بسیار کارا بوده و در سطح وسیعی از پروژه های عمرانی کاربرد دارند. پی های گسترده از انواع پی های سطحی به شمار می روند که ضمن برخورداری از مزایای ذکر شده، ایراداتی از قبیل معضلات اجرایی و نشست های زیاد را نیز به دنبال دارند. با توجه به اهمیت نشست به خصوص نشست های ناهمسان در سازه های بلند و حساس، در صورت تجاوز نمودن مقادیر نشست های متوسط و ناهمسان از حد مجاز، یکی از راه کارهای حذف پی سطحی (رادیه) و استفاده از شمع در زیر سازه و اتکای آن به لایه های سخت و نشست ناپذیر است که علیرغم درجه ی اطمینان بالای آن، دارای مشکلاتی نیز هست. معضلات اجرایی، هزینه ی بالا و احتمال وجود خاک مناسب در اعماق بسیار پایین و نیاز به شمع های بیش تر با طول های بلند و قطر بالا، از جمله این مواردند.
در این خصوص ایده ی تلفیق رادیه و پی های عمیق، به عنوان گزینه ی جدیدی در مبحث پی سازی از دهه ی 70 میلادی مطرح شده است. به کارگیری پی های عمیق در زیر پی های گسترده که اصطلاحاً به سیستم پی گسترده ی مرکب معروف است، می تواند سبب کاهش نشست و اثر توأم افزایش ظرفیت باربری شود. این سیستم در 40 سال اخیر در کشورهای مختلفی از جمله آلمان، اندونزی، ژاپن و ... به کار گرفته شده و اثرات مثبت تلفیق رادیه و شمع در کاهش نشست های کلی و غیر یکنواختِ سازه های بلند و سنگین و نیز کاهش هزینه های اجرایی طرح، سبب رشد تحقیقات علمی در این زمینه و گسترش کاربرد پی های گسترده ی مرکب گردیده است. از این رو شناخت این فونداسیون ها و ارزیابی رفتار آن تحت تأثیر عوامل درونی و بیرونی از مباحث و نیازهای اساسی مهندسی ژئوتکنیک به شمار می رود.
بر خلاف روش های طراحی سنتی شمع و سرشمع (گروه شمع های آزاد) که کل بار روسازه به شمع ها انتقال می یافت، در سیستم رادیه - شمع، هم رادیه و هم شمع های زیرین در باربری مشارکت دارند. در واقع اثر خاک زیرین رادیه و نقش باربری آن در طراحی لحاظ می گردد. از این رو به این سیستم گاهی، پی های گسترده ی مرکب نیز گفته می شود. بدین ترتیب شمع های زیرین برای بار کم تری طراحی شده و دارای ابعاد کوچک تری نسبت به گروه شمع های آزاد خواهند بود. با توسعه ی روش های مختلف تحلیل و طراحی رادیه - شمع ها و شناخت عمیق تر مبانی رفتاری این فونداسیون های مرکب، در روش های جدیدتر، ظرفیت باربری شمع ها به طور کامل بسیج می شود که این امر به معنای ضریب اطمینان یک در طراحی شمع ها است. بدین ترتیب با مشارکت رادیه در برابری و کاهش سهم باربری شمع ها در این سیستم، گروه شمع ها می توانند نقش مؤثرتری در کاهش نشست ها ایفا نمایند. بدیهی است که هرچه سهم باربری شمع ها کم تر و سهم باربری رادیه (خاک) بیش تر باشد، این نقش بیش تر جلوه خواهد کرد. به همین دلیل به این شمع ها، شمع های کاهش دهنده ی نشست نیز گفته می شود (شکل 19).
بر همین اساس شناخت صحیح اندرکنش بین سه المان تشکیل دهنده ی یک پی گسترده مرکب شامل شمع، رادیه و خاک، از عوامل مؤثر در تحلیل، طراحی و کارآیی آن به شمار می رود که البته دلیل اصلی پیچیدگی رفتار این فونداسیون ها و مشکلات مربوط به تحلیل و طراحی نیز از همین مسأله ناشی می گردد (شکل 20). در حالت کلی، بهره گیری از پی های رادیه - شمع سبب کاهش قابل توجه طول شمع ها، بهبود سرویس دهی پی های سطحی به لحاظ نشست های کلی و ناهمسان و طرح اقتصاد فونداسیون ها می گردد که البته در بهینه سازی اثرات مثبت آن، عوامل مختلفی از جمله لایه بندی خاک در عمق، اندرکنش بین شمع - خاک - سازه، اتصال و یا عدم اتصال شمع ها به رادیه، نسبت طول به قطر و فاصله بندی شمع ها نقش اساسی دارند.
بهترین نوع آرایش در حالت بارگذاری گسترده ی یکنواخت به منظور دستیابی به کم ترین مقادیر نشست ماکزیمم و نسبی و همچنین لنگرهای خمشی، متمرکز نمودن شمع ها در 25 درصد مساحت رادیه و در محدوده ی میانی آن می باشد. اگرچه در این حالت، مناسب ترین مقادیر نیروی برشی مربوط به حالتی است که هیچگونه شمعی در زیر رادیه متمرکز شوند. در حالت بارگذاری گسترده ی یکنواخت، تفاوت طول شمع ها و به کارگیری شمع هایی با طول بلندتر در قسمت مرکزی رادیه تأثیر چندانی بر بهینه کردن سیستم نخواهد داشت. در حالت بارگذاری متمرکز، مناسب ترین نوع آزمایش به منظور دستیابی به کم ترین مقادیر نشست ماکزیمم و نسبی و همچنین نمودارهای لنگر خمشی و نیروی برشی زمانیست که شمع هایی با طول بلندتر دقیقاً در زیر بارهای میانی و بقیه شمع های، زیر بارهای کناری رادیه قرار گیرند. تغییر در ضخامت رادیه تأثیر چندانی بر مقادیر نشست ماکزیمم نگذاشته، اما افزایش ضخامت رادیه، سبب کاهش چشم گیر در مقادیر نشست نسبی در دو حالت بارگذاری گسترده ی یکنواخت و متمرکز خواهد شد.
ساختمان Messeturm فرانکفورت از جمله ساختمان هایی است که سیستم پی آن از نوع رادیه - شمع است. کل وزن ساختمان به قرار MN 1900 بوده که با احتساب زیر فشار مقدار خالص آن به قرار MN 1700 می باشد. مقطع عرض برج مربعی به ضلع m 41 بوده در حالی که برای پی گسترده ی آن مربعی به ضلع m 60 منظور شده است. از آن جا که نشست پی گسترده ی بدون شمع به قرار mm 400 برآورد شده بود، سیستم پی رادیه با شمع انتخاب شده تا میزان نشست به نصف مقدار فوق تقلیل یابد. وقوع نشست های نسبتاً زیاد، احتمال چرخش و ضریب لاغری ساختمان به قرار 4 منجر به تصمیم گیری در انتخاب پی گسترده ی مرکب شده است. 64 شمع در قالب سه دایره ی متحدالمرکز مطابق شکل 21 به کار گرفته شدند.
ضخامت پی گسترده در مرکز به قرار m6 و در لبه ها به m3 تقلیل یافته است. استفاده از شمع ها باعث تقلیل مقدار نشست به mm150 شده است. نتایج حاصله ی در شکل 22 نشان می دهد که سهم مشارکت پی گسترده و شمع ها به ترتیب به قرار 45 درصد و 55 درصد در تحلیل بار قابل توجه بوده، که حاکی از بهینه بودن طراحی سیستم فونداسیون مرکب انتخابی می باشد.
جمع بندی و نتیجه گیری
با پیشرفت روز افزون تکنولوژی، روش های تحلیل و طراحی ابنیه ی ژئوتکنیکی از قبیل پی های عمیق نیز از سیمای جدیدتر و البته دقیق تری برخوردار می شوند. روش های تحلیل قدیمی به آرامی جای خود را به روش های نوین و بدیع امروزی داده تا در نهایت شاهد هر چه کامل تر، مقرون به صرفه تر و سریع تر بودن روند تحلیل و طراحی این دسته از پی ها باشیم. در زیر به طور خلاصه به جمع بندی و نتیجه گیری مباحث پیشین می پردازیم:
- کاربرد پی های عمیق مختص پروژه های خاص و با اهمیت و در صورت وجود شرایط خاک نامناسب در بستر می باشد. استفاده از این نوع فونداسیون ها در صنعت ساختمان سازی، موجب افزایش سرعت اجرا، افزایش ضریب اطمینان در مقابل واژگونی، افزایش عمر مفید سازه و تضمین سرمایه گذاری ها می باشد.
- ظرفیت باربری شمع ها از دو جنبه ی مقاومت ژئوتکنیکی و مقاومت سازه ای حایز اهمیت می باشد. مقاومت ژئوتکنیکی یا ظرفیت باربری، باری است که موجب گسیختگی خاک اطراف و کف شمع می گردد. از متدهای متداول جهت تعیین توان باربری شمع ها می توان روش های آنالیز استاتیکی، آنالیز استاتیکی با استفاده از نتایج تست های درجا، آنالیز دینامیکی و تست های دینامیکی و آزمایش بارگذاری استاتیکی را نام برد.
- روش های استاتیکی در تعیین ظرفیت باربری به علت عواملی از قبیل پیچیدگی رفتار خاک، دشواری در تعیین پارامترهای واقعی خاک در اعماق و اصول، مبانی و مفروضات هر روش همواره تحت تأثیر قرار دارند. از جمله ی آن ها می توان به وابستگی ضریب Nq به زاویه ی اصطکاک داخلی به دست آمده از آزمایشات آزمایشگاهی اشاره نمود.
- از جمله ی روش های آیین نامه ای مرسوم می توان روش متحد در تعیین ظرفیت باربری شمع ها را نام برد. با توجه به تنوع روش ها و توصیه ها در خصوص مقادیر rs¬ و rt و نیز روابط مختلف Nq بر حسب ، رویه ای یکنواخت تحت عنوان روش متحد معرفی شد.
- آزمایش بارگذاری استاتیکی شمع را می توان مستقیم ترین و کامل ترین روش تعیین ظرفیت باربری یک شمع دانست. به دلیل وجود موارد عدم اطمینان متعدد در روند آنالیز و طراحی شمع ها، انجام شدن این آزمایش بر روی شمع های در ابعاد واقعی به صورت یک امر ضروری در اکثر پروژه های مهم درآمده است. نتایج به دست آمده از آزمایش بارگذاری شمع به صورت یک نمودار بار - تغییر مکان ارائه می شود.
- به علت عدم قابل اطمینان بودن روش های استاتیکی به دلایل مذکور، استفاده از نتایج آزمایش های درجا (از قبیل CPTu) به عنوان یک آلترناتیو و مکمل روش های تحلیل استاتیکی در تعیین توان باربری پی های عمیق در سه دهه ی اخیر پیشرفت رو به رشدی داشته است. با استفاده از داده های خروجی آزمایش CPTu (qc، fs و u2) و استفاده از روش های نرم افزاری که در دهه های اخیر توسعه ی چشم گیری را داشته اند می توان بدون وابستگی به پارامترهای خاک به تعیین ظرفیت باربری شمع دست یافت.
- در مجموع سه روش دینامیکی شامل فرمول های دینامیکی، آنالیز دینامیکی و تست های دینامیکی و توأم با آنالیز دینامیکی جهت تعیین توان باربری شمع ها با روش های دینامیکی مرسوم اند. روش آزمایشی PDA روشی بسیار کارآمد در اندازه گیری ظرفیت باربری می باشد.
- علاوه بر تعیین توان باربری ژئوتکنیکی، شمع ها باید به لحاظ سازه ای و مصالح موجود در آن ها بارهای خارجی را با عکس العمل مناسب داخل تحمل نمایند که اصطلاحاً به آن مقاوم سازه ای گفته می شود. در شرایط متعارف، در صورتی که تنها بار محوری مطرح باشد، مقطع بحرانی برای شمع از لحاظ طرح سازه ای محل صفحه ی خنثی است. زیرا علاوه بر بارهای سرویس وارده به راس شمع، افزایش نیروی محوری در شمع ناشی از نیروهای پس ماند (مسأله ی اصطکاک منفی)، در محل صفحه ی خنثی به حداکثر می رسد.
- کنترل نشست برای شمع ها ضروری است. گرچه اغلب مواقع شمع ها به عنوان یک روش برای اجتناب از نشست بالای پی های سطحی به کار می روند و تصور برخی بر این است که شمع ها دچار نشست نخواهند شد، اما در مورد شمع های اصطکاکی و به خصوص شمع هایی که در زیر صفحه ی خنثی آن ها لایه های نشست پذیر وجود دارد، حتماً بایستی با دقت کنترل گردند. البته باید توجه داشت که مسأله ی نشست در شمع ها نسبت به مسأله ی ظرفیت باربری از اهمیت کم تری برخوردار می باشد.
- برای تعیین بار مجاز روی شمع معمولاً بار نهایی با ظرفیت باربری شمع به ضریب اطمینان تقسیم می شود. مقدار ضریب اطمینان به ریسک پذیری عواقب مربوط به خرابی سازه و میزان دانش و آگاهی نسبت به بارهای وارده دارد. در صورت استفاده از چند روش ترکیبی برای تعیین ظرفیت باربری، می توان مقدار ضریب اطمینان را که به طور سنتی معادل 3 تا 4 در پی های عمیق مطرح است به حدود 5/1 تا 2 کاهش داد. بنابراین مشاهده می گردد که انتخاب مناسب ضریب اطمینان تا چه میزان در اقتصاد پروژه و مقرون به صرفه بودن آن مؤثر می باشد.
- به کارگیری پی های عمیق در زیر پی های گسترده که اصطلاحاً به سیستم پی گسترده ی مرکب معروف است، می توانند سب کاهش نشست و اثر توام افزایش ظرفیت باربری شود. بهترین نوع آرایش در حالت بارگذاری گسترده ی یکنواخت به منظور دستیابی به کم ترین مقادیر نشست، متمرکز نمودن شمع ها در 25 درصد مساحت رادیه و در محدوده ی میانی آن می باشد. در حالت بارگذاری متمرکز، بر خلاف بارگذاری گسترده ی یکنواخت، تفاوت طول شمع ها و به کارگیری شمع هایی با طول بلندتر در قسمت مرکزی رادیه سبب رسیدن به کم ترین مقدار نشست خواهد شد. در حالت بارگذاری متمرکز، به کارگیری شمع هایی با طول بلندتر در قسمت مرکزی رادیه و زیر بارهای متمرکز نسبت به شمع های کناره ها، سبب رسیدن به کم ترین مقدار نشست و لنگر خمشی و نیروی برشی در رادیه خواهد شد.
پینوشتها:
1- Piled – Raft Foundations
منابع و مراجع:
1- اسلامی، ابوالفضل. 1385، «مهندسی پی، طراحی و اجرا»، مرکز تحقیقات ساختمان مسکن، چاپ سوم - نشریه ی 437.
2- اسلامی، ابوالفضل، 1385، «پی های گسترده؛ تحلیل، طراحی و عملکرد»، انتشارات دانشگاه گیلان.
3- «روش های مختلف تعیین توان باربری محوری شمع ها و دستورالعمل های اجرایی»، 1384- مرکز تحقیقات و آموزش وزارت راه و ترابری؛ توسط فخاریان، کاظم و اسلامی، ابوالفضل.
4- Briaud, J. L., and Tucker, L. M., 1988. Measured and predicted axial capacity of 98 Piles. American Society OF Civil Engineers, ASCE, Journal of Geotechnical Engineering, Vol. 114, No .9, pp. 984-1001.
5- Budhu, M, 2007. Soil Mechanics and Foundations, 586p.
6- Burland, J. B. and Burbidge, M.C., 1982. Settlement of Foundation on Sand and Gravel, Proc. Instn. Civil Engrs. December, 78 (Part 1), pp. 1325-1381.
7- Campanella, R.G and Robertson, P.K., 1982. State of the Art in In Situ Testing of Soils, Proceedings, Engineering Foundation Conference on Updating Subsurface Sampling of SOILS AND Rocks, and Their In Situ Testing. Santa Barbara, Califomia, 23P.
8- CFEM, Canadian Foundation Engineering Manual, 1992.
9- Coduto, D. P., 2001. Foundation Design Principles and Practices, Prentice-Hall, Inc, 370p.
10- DFI, 2006 Deep Foundation Institute, 31 th Annual Conference on Deep Foundations.
11- Eslami, A., and Fellenius, B. H., 1997. Pile capacity by direct CPT and CPTu methods applied to 102 case histories. Canadian Geotechnical Journal, December, Vol 34, No 6, Eslami, A., pp886-904.
12- Fang, H. Y., 2001, Foundation Engineering Handbook. 2nd Edition, CBS, 923p.
13- Fellenius, B. H., 2001. The O-Cell An innovative engineering tool. Geotechnical News Magazine, Vol. 19, No.2pp 32-33.
14- Fellenius, B. H., Eslami, A, and Infante, J. A. 2002. Unicone, a program for Processing and Reporting of Cone Penetration Tests (CPT and CPTu), Soil Profiling and pile Capacity Analysis. UniSoft Ltd., 1905 Alexander Street, Calgary, Alberta, T2G 4J3.
15- GRL, 1995. Goble, Raushe and Linkins, Wave Equation Analysis of pile driving, Vols. 1-4, Cleeveland, 355 p.
16- Hemsley, J. A., 2000. Design applications of raft foundations, Tomas Telford, 626p.
17- Shariatmadari, N. Eslami, A. and Karimpour-Fard, M. 2007. Bearing Capacity of Driven Piles In Sands From SPT-Appleid to 60 Case.
18- Poulos. H.G and. Davis, E. D, 1980. Pile Foundation Analysis & Design. 397p.
19- Van Impe, W. F., 1994 Developments in pile design- 4th International DFI Conference.